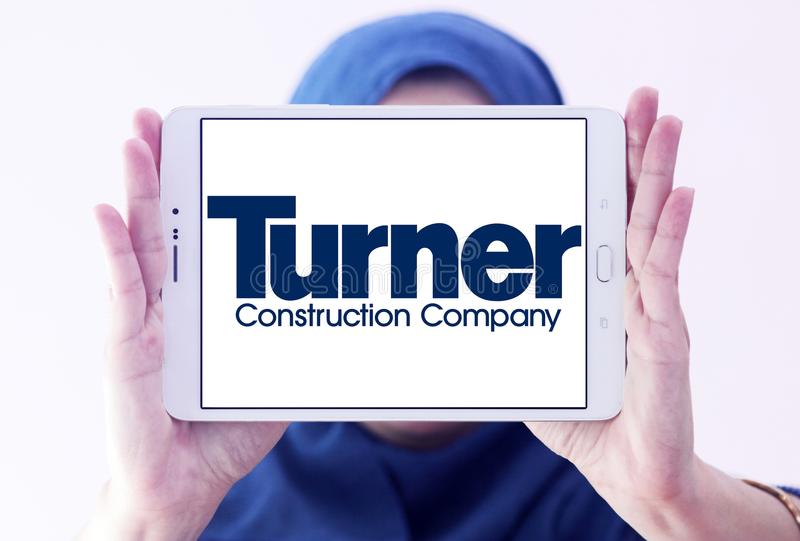
Logistics is the movement, storage, and distribution of goods from initial production to final delivery. The logistics industry involves many organizations, people, activities, and information to make goods available for purchase. A logistics supply chain involves multiple stakeholders. Although logistics is the main focus of many companies' operations, the process can incorporate other components such as transport and software. These are some of the various types of logistical systems. Continue reading to find out more about these systems, and how they can help improve your supply chain operations.
Logistics refers to the movement, storage and distribution of goods, starting with initial production until final delivery.
Logistics refers to the efficient movement of goods from their initial production through final delivery. The optimal flow optimization ensures products reach their customers in the most efficient manner. Here are 7 rights of logistics. The first is to arrive at the right time. Customers should receive products at the correct time and in the right conditions.
Inbound logistic focuses only on the inbound movements of products and materials to manufacturers. Outbound Logistics focuses on outbound flows of goods and information that come from sources other than the business. Inbound logistics focuses on acquiring materials and arranging inbound transportation, storage, and distribution to customers. Reverse logistics is the return shipment and packaging of finished products. It also includes the management of remaining inventory and, in certain cases, the disposal and reuse of waste.
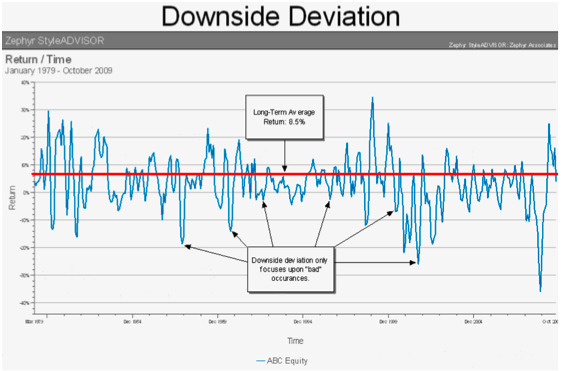
It is a risk-adjusted enterprise
The concept of a risk-adjusted investment (RAR) describes the use of funds or capital that takes on a greater degree of risk than a normal business investment. The difference between risk-adjusted investments and the yields of normal business investments is called the opportunity cost of risk. In addition to reducing the risk of investments, RAR can help business owners manage their cash flows across different functional areas of the business.
It is a limited part of a larger, collaborative supply chain
A highly integrated supply chain is a highly interdependent network of suppliers that rely on timely deliveries of quality components. In this type of supply chain, failures to deliver could lead to the complete stoppage of the chain. Even the best logistics providers or suppliers can't avoid all disruptions. To ensure smooth and efficient operation of the chain, it is vital that everyone evaluates the potential risks involved in any given system.
Collaborating with retailers and manufacturers can make a difference for both of them. One example of this is a recent partnership between a retailer with a major U.S. chain retail store. It resulted in lower logistics costs between the factory's warehouse and the store. Collaborations in this area can also help retailers increase their sales. To reduce transport and labor costs between factory and store, manufacturers and retailers can work together.
It involves software
Supply management software can help companies manage their entire supply network. The software can manage all aspects, from vendor relationships through to transactions. Supply chain management software should be used regardless of whether you run a small business or large corporation. These software programs allow you to manage your inventory, supplier relationships, as well as the flow of data throughout your organization. These programs could include all stages of product design, from warehousing to shipping. They can also manage inventory and provide insight into trends and demand.
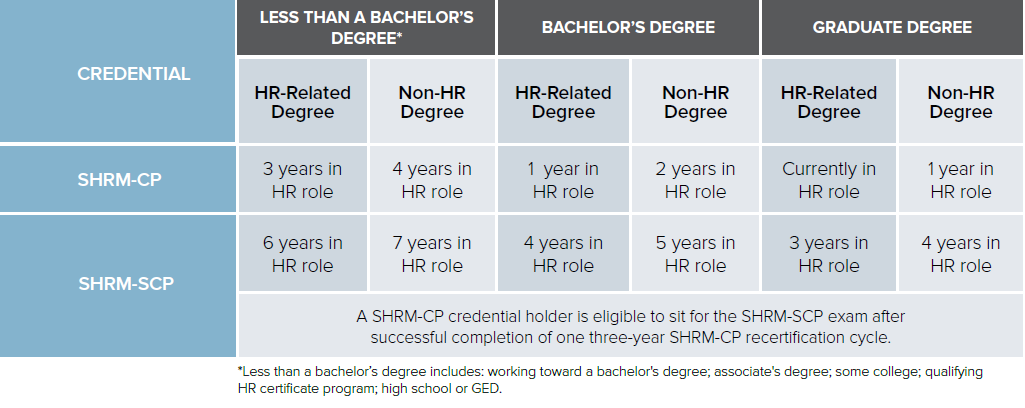
Use of logistics software allows for improved inventory management, fleet management, and simplified communication. It can also help improve customer service. It automates everyday tasks and provides actionable insights to business owners. It improves communication and inventory processes which are essential to the success of supply chain management. These software applications can improve customer service and increase profitability. If you're considering buying software for your enterprise you might be curious what the benefits are.
FAQ
How can a manager motivate employees?
Motivation refers to the desire or need to succeed.
Enjoyable activities can motivate you.
Or you can get motivated by seeing yourself making a contribution to the success of the organization.
For example, if your goal is to become a physician, you will probably find it more motivational to see patients rather than to read a lot of medicine books.
Another type of motivation comes from within.
Perhaps you have a strong sense to give back, for example.
You may even find it enjoyable to work hard.
If you feel unmotivated, ask yourself why.
Then, consider ways you could improve your motivation.
Why does it sometimes seem so hard to make good business decisions
Complex business systems have many moving parts. Their leaders must manage multiple priorities, as well as dealing with uncertainty.
The key to making good decisions is to understand how these factors affect the system as a whole.
It is important to consider the functions and reasons for each part of the system. Then, you need to think about how these pieces interact with one another.
You need to ask yourself if your previous actions have led you to make unfounded assumptions. If you don't have any, it may be time to revisit them.
Asking for assistance from someone else is a good idea if you are still having trouble. You might find their perspective is different from yours and they may have insight that can help you find the solution.
What is Six Sigma, exactly?
It's a method for quality improvement that focuses on customer service as well as continuous learning. This is an approach to quality improvement that uses statistical techniques to eliminate defects.
Motorola created Six Sigma as part of their efforts to improve manufacturing processes in 1986.
The idea spread quickly in the industry. Today many organizations use six-sigma techniques to improve product design.
What is the difference between leadership and management?
Leadership is all about influencing others. Management is about controlling others.
A leader inspires followers while a manager directs workers.
Leaders inspire people to achieve success. Managers keep their workers focused.
A leader develops people; a manager manages people.
Statistics
- Your choice in Step 5 may very likely be the same or similar to the alternative you placed at the top of your list at the end of Step 4. (umassd.edu)
- 100% of the courses are offered online, and no campus visits are required — a big time-saver for you. (online.uc.edu)
- The profession is expected to grow 7% by 2028, a bit faster than the national average. (wgu.edu)
- This field is expected to grow about 7% by 2028, a bit faster than the national average for job growth. (wgu.edu)
- UpCounsel accepts only the top 5 percent of lawyers on its site. (upcounsel.com)
External Links
How To
How do you implement a Quality Management Plan (QMP)?
QMP (Quality Management Plan) is a system to improve products and services by implementing continuous improvement. It emphasizes on how to continuously measure, analyze, control, and improve processes, product/service, and customer satisfaction.
The QMP is a standard method used to ensure good business performance. The QMP aims to improve the process of production, service delivery, and customer relationship. QMPs should encompass all three components - Products and Services, as well as Processes. When the QMP includes only one aspect, it is called a "Process" QMP. QMPs that focus on a Product/Service are known as "Product" QMPs. QMP is also used to refer to QMPs that focus on customer relations.
When implementing a QMP, there are two main elements: Scope and Strategy. These elements are as follows:
Scope: This describes the scope and duration for the QMP. For example, if your organization wants to implement a QMP for six months, this scope will define the activities performed during the first six months.
Strategy: This is the description of the steps taken to achieve goals.
A typical QMP is composed of five phases: Planning Design, Development, Implementation and Maintenance. Each phase is described below:
Planning: In this stage, the objectives of the QMP are identified and prioritized. In order to fully understand and meet the needs of all stakeholders involved in this project, they are consulted. After identifying the objectives, priorities and stakeholder involvement, it's time to develop the strategy for achieving the goals.
Design: This stage is where the design team creates the vision, mission and strategies necessary for successful implementation of QMP. These strategies are implemented by the development of detailed plans and procedures.
Development: Here, the development team works towards building the necessary capabilities and resources to support the implementation of the QMP successfully.
Implementation: This involves the actual implementation of the QMP using the planned strategies.
Maintenance: It is an ongoing process that maintains the QMP over time.
The QMP must also include several other items:
Stakeholder involvement is important for the QMP's success. They are required to actively participate in the planning, design and development of the QMP, as well as the implementation and maintenance phases.
Project Initiation. It is important to understand the problem and the solution in order to initiate any project. The initiator must know the reason they are doing something and the expected outcome.
Time frame: It is crucial to know the time frame for the QMP. If you plan to implement the QMP for a short period, you can start with a simple version. If you're looking to implement the QMP over a longer period of time, you may need more detailed versions.
Cost Estimation: Another important component of the QMP is cost estimation. Planning is not possible without knowing the amount of money you will spend. Therefore, cost estimation is essential before starting the QMP.
QMPs are not only a document, but also a living document. This is the most important aspect of QMPs. It changes with the company. So, it should be reviewed periodically to make sure that it still meets the needs of the organization.