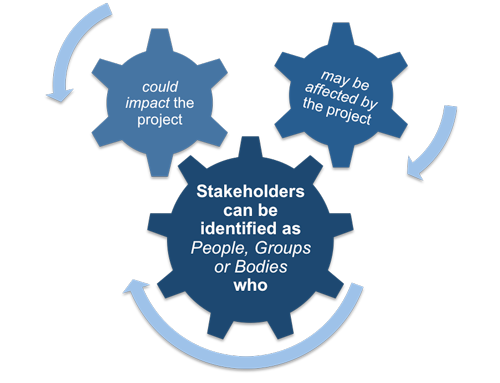
Supply chain management courses are offered by universities around the world. These courses can help you learn about the theories, principles, and methods involved in the field. In addition, they can give you the skills you need to manage your business. You can even become certified in the field. Depending on your interests, you have the option of studying at university, online, and in private training centers.
Concepts
In Supply Chain Management courses, students will learn about the processes and techniques used to plan, implement, and manage a company's entire supply chain. They will also be able to apply concepts like purchasing, quality control, and lean management to their supply chain. Students will also learn the different types of analytics that are used in supply chains today and how they can be applied to various business situations. Students will learn all about stochasticity, lead times, queue psychology and design of logistics.
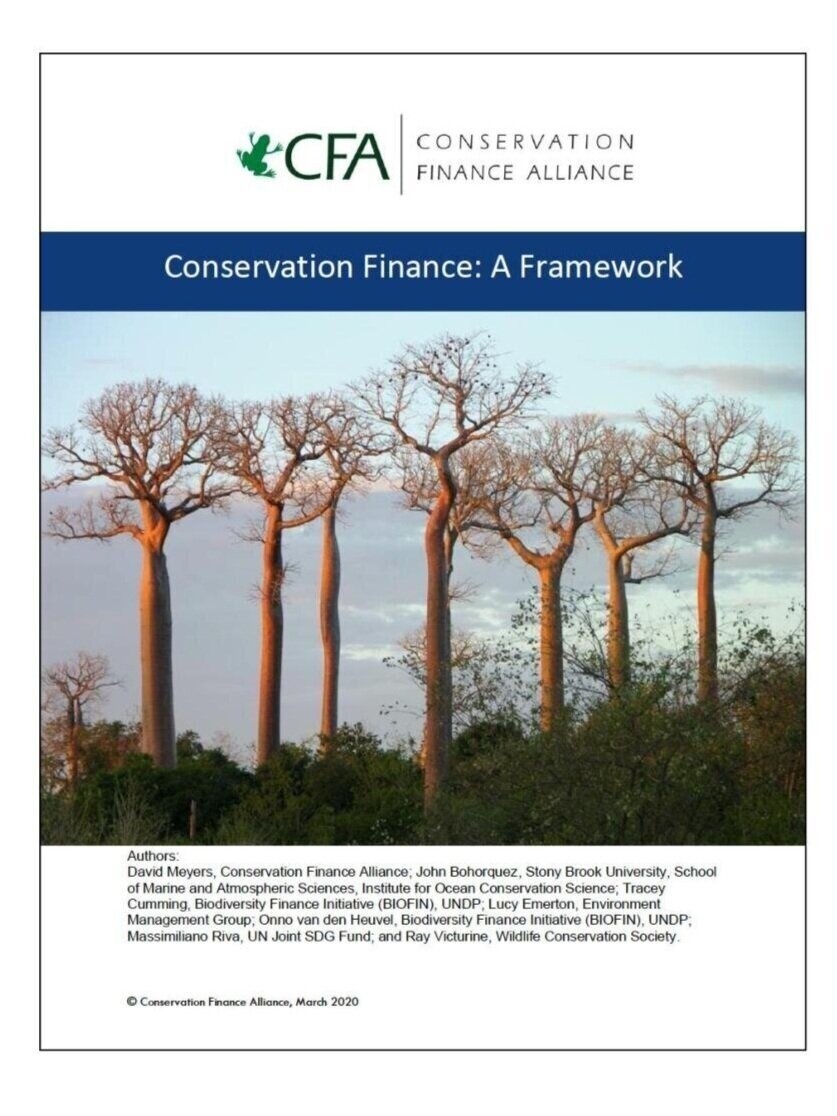
Principles
These principles will help you to manage your business effectively so that goods and services are always available and in good condition. Supply chain management involves planning, designing, and managing the entire supply chains. Supply chain management principles can help businesses meet their customer needs and reduce costs.
Methodologies
Methodologies of supply chain management courses cover the latest trends and techniques for successful supply chains. These courses help students understand the importance of data-driven analytics and their role in providing prescriptive actions. The students learn how to apply data driven analysis tools to three real supply-chain projects. They learn about customer-supplier relationships as well as ethical considerations.
Costs
Companies must create strategies and tactical plans to optimize their operations in order to control the supply chain costs. They must also make decisions to reduce costs and improve productivity. These decisions can impact the company’s bottom line. These are the goals of supply chain management courses.
Internships
Internships as supply chain managers are a great way of gaining valuable experience in a business environment and to develop your skills. These internships provide a low-risk, high reward opportunity to learn basics of supply chain administration while working for a well-respected company. You'll be able to observe the workings of large businesses, meet senior leaders, and take part in several projects. Additionally, you will gain invaluable hands-on experience in business operations and logistics.
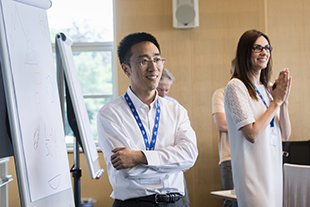
Requirements
You will need to be able to meet the prerequisites to pursue a career supply chain management. You need to be familiar with operations management and statistics before you enroll in a course. Also, you must be comfortable with working with a computer. Online courses in supply chain management can only be taken by those who have reliable internet access.
FAQ
What are the steps to take in order to make a management decision?
The decision-making process of managers is complicated and multifaceted. This involves many factors including analysis, strategy and planning, implementation, measurement and evaluation, feedback, feedback, and others.
The key thing to remember when managing people is that they are human beings just as you are and therefore make mistakes. You are always capable of improving yourself, and there's always room for improvement.
In this video, we explain what the decision-making process looks like in Management. We discuss different types of decisions as well as why they are important and how managers can navigate them. The following topics will be covered.
What are the four major functions of Management?
Management is responsible for organizing, managing, directing and controlling people, resources, and other activities. This includes setting goals, developing policies and procedures, and creating procedures.
Organizations can achieve their goals through management. This includes leadership, coordination, control and motivation.
Management has four primary functions:
Planning – Planning involves deciding what needs to happen.
Organizing: Organizing refers to deciding how things should work.
Directing - This refers to getting people follow instructions.
Controlling: Controlling refers to making sure that people do what they are supposed to.
What is the difference between Six Sigma Six Sigma and TQM?
The main difference in these two quality management tools lies in the fact that six sigma is focused on eliminating defects and total quality management (TQM), emphasizes improving processes and reducing costs.
Six Sigma is an approach for continuous improvement. It emphasizes the elimination or minimization of defects through statistical methods such control charts and p charts.
This method seeks to decrease variation in product output. This is done by identifying root causes and rectifying them.
Total quality management includes monitoring and measuring all aspects of an organization's performance. Training employees is also part of total quality management.
It is commonly used as a strategy for increasing productivity.
Statistics
- The average salary for financial advisors in 2021 is around $60,000 per year, with the top 10% of the profession making more than $111,000 per year. (wgu.edu)
- UpCounsel accepts only the top 5 percent of lawyers on its site. (upcounsel.com)
- This field is expected to grow about 7% by 2028, a bit faster than the national average for job growth. (wgu.edu)
- The profession is expected to grow 7% by 2028, a bit faster than the national average. (wgu.edu)
- 100% of the courses are offered online, and no campus visits are required — a big time-saver for you. (online.uc.edu)
External Links
How To
How can you implement the Kaizen technique?
Kaizen means continuous improvement. Kaizen is a Japanese concept that encourages constant improvement by small incremental changes. It's a team effort to continuously improve processes.
Kaizen is one of Lean Manufacturing's most efficient methods. The concept involves employees responsible for manufacturing identifying problems and trying to fix them before they become serious issues. This way, the quality of products increases, and the cost decreases.
Kaizen is an approach to making every worker aware and alert to what is happening around them. So that there is no problem, you should immediately correct it if something goes wrong. So, if someone notices a problem while working, he/she should report it to his/her manager.
When doing kaizen, there are some principles we must follow. When working with kaizen, we always start with the end result and move towards the beginning. In order to improve our factory's production, we must first fix the machines producing the final product. Then, we fix the machines that produce components and then the ones that produce raw materials. Then we fix the workers, who directly work with these machines.
This method is known as kaizen because it focuses upon improving every aspect of the process step by step. After we're done with the factory, it's time to go back and fix the problem.
Before you can implement kaizen into your business, it is necessary to learn how to measure its effectiveness. There are many methods to assess if kaizen works well. One way is to examine the amount of defects on the final products. Another way to find out how productive your company has been since you implemented kaizen is to measure the increase in productivity.
You can also find out if kaizen works by asking yourself why you decided to implement it. You were trying to save money or obey the law? It was a way to save money or help you succeed.
Suppose you answered yes to any of these questions, congratulations! You're ready to start kaizen.