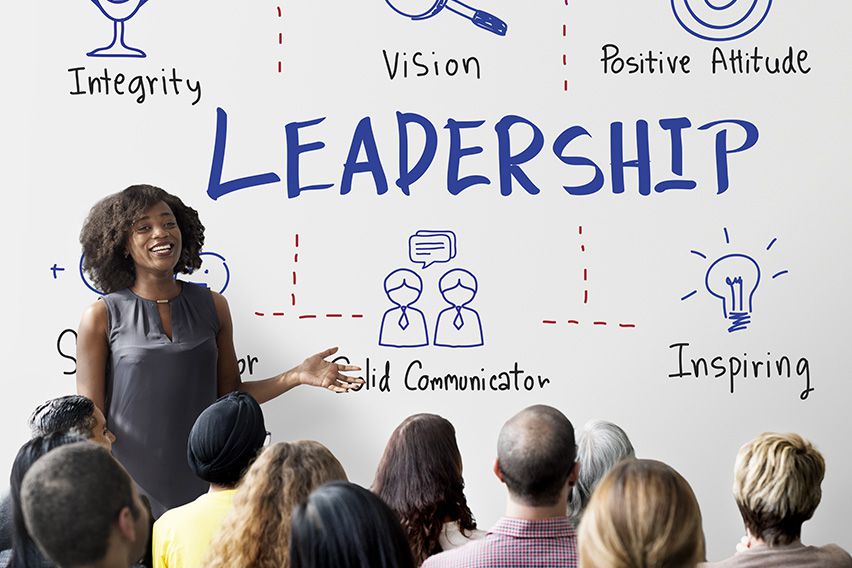
There are many ways that brand management can be accomplished. A superior product or service can make a company's brand strong. They also help to build brand awareness through traditional and online marketing channels. Business strategy is incomplete without brand management. Any company needs to build and maintain a strong brand in order to attract customers. Leaders recognize the importance of brand awareness, and they use multiple marketing channels to reach a wide audience.
Indirect Brand Management
A process that develops and establishes a brand for a product, or service is known as branding management. It involves marketing, creating and measuring brand components. These include recall, preference, recognition and recognition. Direct brand administration focuses on the product or service's physical appearance, price and other aspects. Indirect branding management focuses only on its intangible assets. To be effective, a brand manager needs to know the brand's positioning value and customer perception.
Indirect branding management can help to establish a brand identity for a product. It involves maintaining a positive impression among consumers and ensuring that they have a positive experience using the product. The company will be able to increase sales and build a loyal customer base. The main objective of brand management is to maintain a positive image of the brand among existing and potential customers.
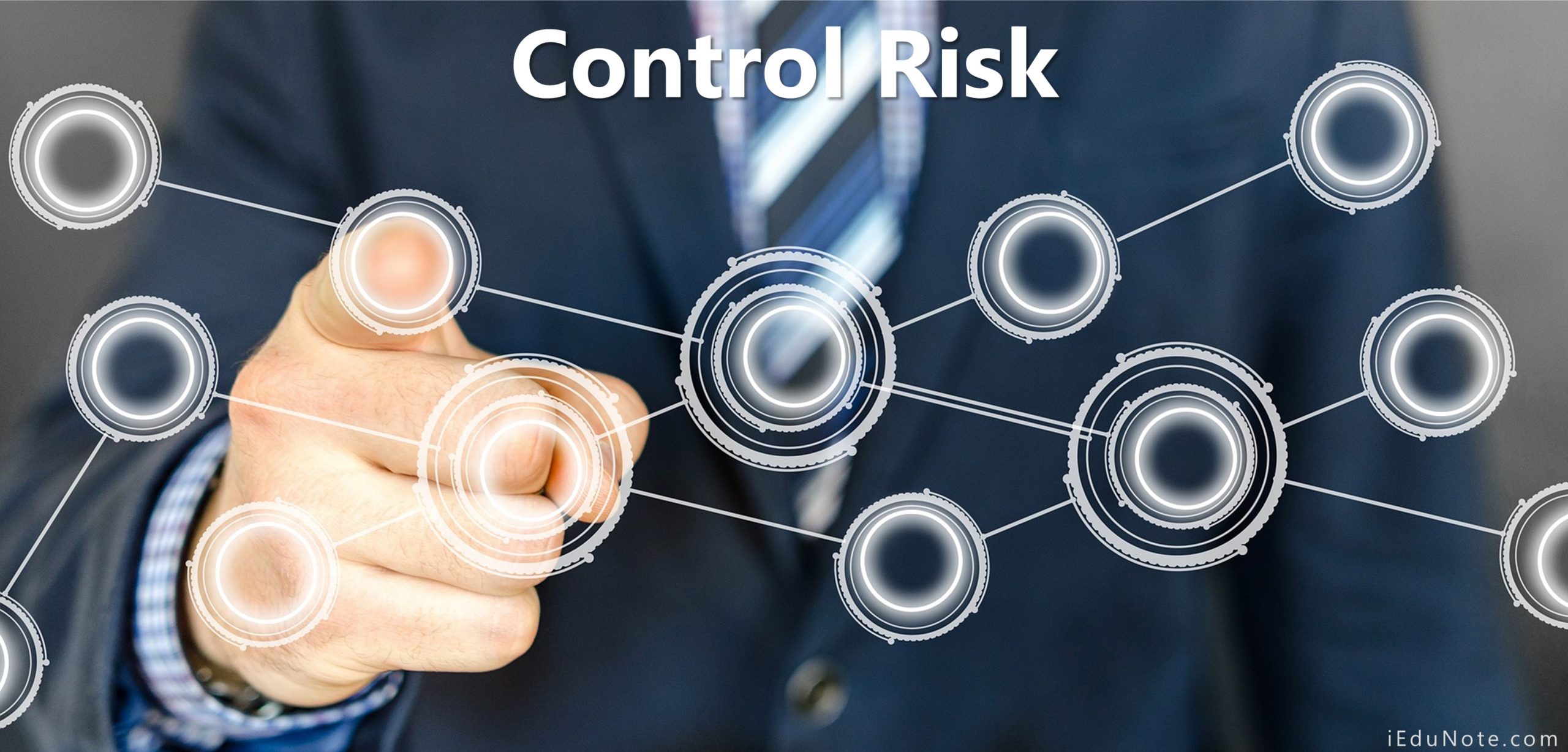
Brand building
Brand building is a process that makes brands memorable. You must first understand your target market to build a brand. Then, you can create marketing materials and website content that are tailored to those needs. A brand can take time to establish a loyal following. Therefore, you should be patient when building your reputation.
Businesses can also build brand loyalty and help attract new customers. Customers who have known and trusted a brand for many years are more likely purchase their product again. And, new customers are more likely and more willing to try it. A strong brand will allow you to establish a strong presence within your industry. This will result in increased sales.
Brand equity
Brand management is only possible if you have brand equity. It determines the market share and represents the brand's worth. A strong brand equity will help your brand establish itself in the market, survive a crisis, and perform well in the long run. The concept of brand equity first appeared in marketing literature back in the 1980s. Today, it is a multidimensional concept and can be applied to many aspects in brand management.
The study of brand equity has revealed that there are many factors that can impact it, including product features, brand values, and brand perception. The country from which the brand is made can also have an impact on brand equity. Research has shown that the country of origin can influence a brand’s perception of quality and loyalty.
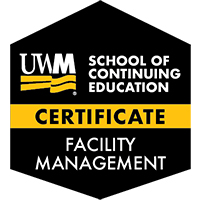
Reputation for your brand
Management of your brand reputation is an essential part of building a strong brand. It allows you to establish a brand identity and guide your actions in specific situations. This will help your company to build brand loyalty as well as revenue streams. You can boost your brand reputation by using the following strategies: Content Marketing You can increase brand awareness by creating educational content about your brand or products.
The process of building your brand reputation is ongoing. The first step is to evaluate your company's image. Even though your company may already be well-respected, it is a smart idea to first assess the strengths and weaknesses of the company. You can then tailor the plan for your business.
FAQ
What are the three main management styles you can use?
There are three main management styles: participative, laissez-faire and authoritarian. Each style has its strengths and weaknesses. Which style do YOU prefer? Why?
Autoritarian - The leader sets direction and expects everyone else to follow it. This style works best in large organizations that are stable and well-organized.
Laissez-faire is a leader who allows everyone to make their own decisions. This style works best when an organization is small and dynamic.
Participative - The leader listens to ideas and suggestions from everyone. This is a great style for smaller organizations that value everyone.
What is the difference between TQM and Six Sigma?
The major difference between the two tools for quality management is that six Sigma focuses on eliminating defect while total quality control (TQM), on improving processes and decreasing costs.
Six Sigma is a method for continuous improvement. It emphasizes the elimination of defects by using statistical methods such as control charts, p-charts, and Pareto analysis.
This method aims to reduce variation in product production. This is accomplished by identifying the root cause of problems and fixing them.
Total quality management includes monitoring and measuring all aspects of an organization's performance. Training employees is also part of total quality management.
It is commonly used as a strategy for increasing productivity.
It seems so difficult sometimes to make sound business decisions.
Complex systems and many moving parts make up businesses. They require people to manage multiple priorities and deal with uncertainty and complexity.
Understanding the impact of these factors on the system is crucial to making sound decisions.
To do this, you must think carefully about what each part of the system does and why. Next, consider how each piece interacts with the others.
You need to ask yourself if your previous actions have led you to make unfounded assumptions. You might consider revisiting them if they are not.
You can always ask someone for help if you still have questions after all of this. You might find their perspective is different from yours and they may have insight that can help you find the solution.
Statistics
- Your choice in Step 5 may very likely be the same or similar to the alternative you placed at the top of your list at the end of Step 4. (umassd.edu)
- Hire the top business lawyers and save up to 60% on legal fees (upcounsel.com)
- Our program is 100% engineered for your success. (online.uc.edu)
- The profession is expected to grow 7% by 2028, a bit faster than the national average. (wgu.edu)
- The average salary for financial advisors in 2021 is around $60,000 per year, with the top 10% of the profession making more than $111,000 per year. (wgu.edu)
External Links
How To
What is Lean Manufacturing?
Lean Manufacturing uses structured methods to reduce waste, increase efficiency and reduce waste. They were created in Japan by Toyota Motor Corporation during the 1980s. The primary goal was to make products with lower costs and maintain high quality. Lean manufacturing eliminates unnecessary steps and activities from a production process. It is made up of five elements: continuous improvement, continuous improvement, just in-time, continuous change, and 5S. Pull systems involve producing only what the customer wants without any extra work. Continuous improvement is constantly improving upon existing processes. Just-in-time is when components and other materials are delivered at their destination in a timely manner. Kaizen stands for continuous improvement. Kaizen can be described as a process of making small improvements continuously. Last but not least, 5S is for sort. To achieve the best results, these five elements must be used together.
Lean Production System
Six key concepts make up the lean manufacturing system.
-
Flow: The goal is to move material and information as close as possible from customers.
-
Value stream mapping: This is a way to break down each stage into separate tasks and create a flowchart for the entire process.
-
Five S's – Sort, Put In Order Shine, Standardize and Sustain
-
Kanban - use visual signals such as colored tape, stickers, or other visual cues to keep track of inventory;
-
Theory of constraints: Identify bottlenecks and use lean tools such as kanban boards to eliminate them.
-
Just-in time - Get components and materials delivered right at the point of usage;
-
Continuous improvement: Make incremental improvements to the process instead of overhauling it completely.