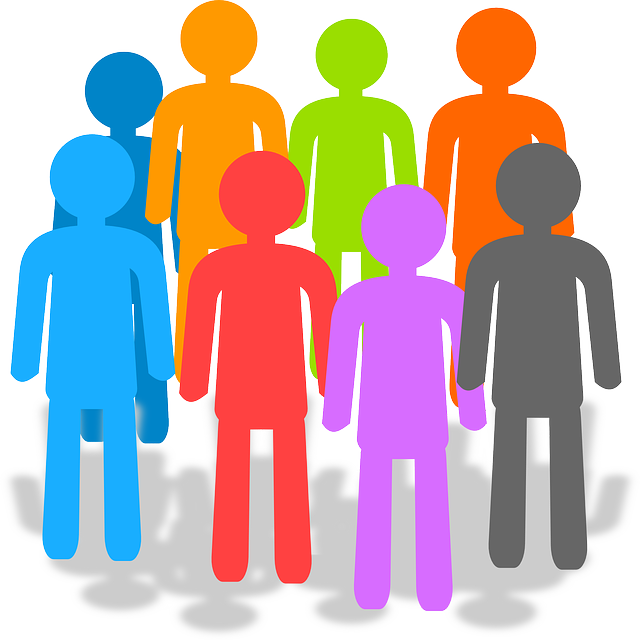
Organizations are increasingly focusing on promoting supply diversity. Companies are focusing on promoting supplier diversity for a variety of reasons, including customer sentiment, competition and cost control. Diverse suppliers are likely to be more flexible and capable of meeting customer needs sooner than larger suppliers. Aside from being able to tailor solutions, they can reduce costs.
Sources for supplier diversity
Companies must look for diverse suppliers as a way to increase the number of minority-owned companies. Companies are developing supplier diversity plans. These programs allow minority-owned businesses to source their products and services. Supplier diversity partners must be a part of the company's values and commitment to inclusion.
Both businesses and communities can benefit from supplier diversity programs. Many large companies actively encourage and require diversity initiatives. Target is one example. In 2019, Target invested $1.4 Billion in diverse suppliers. It has also encouraged first-tier suppliers to purchase contributions from second-tier diverse suppliers.
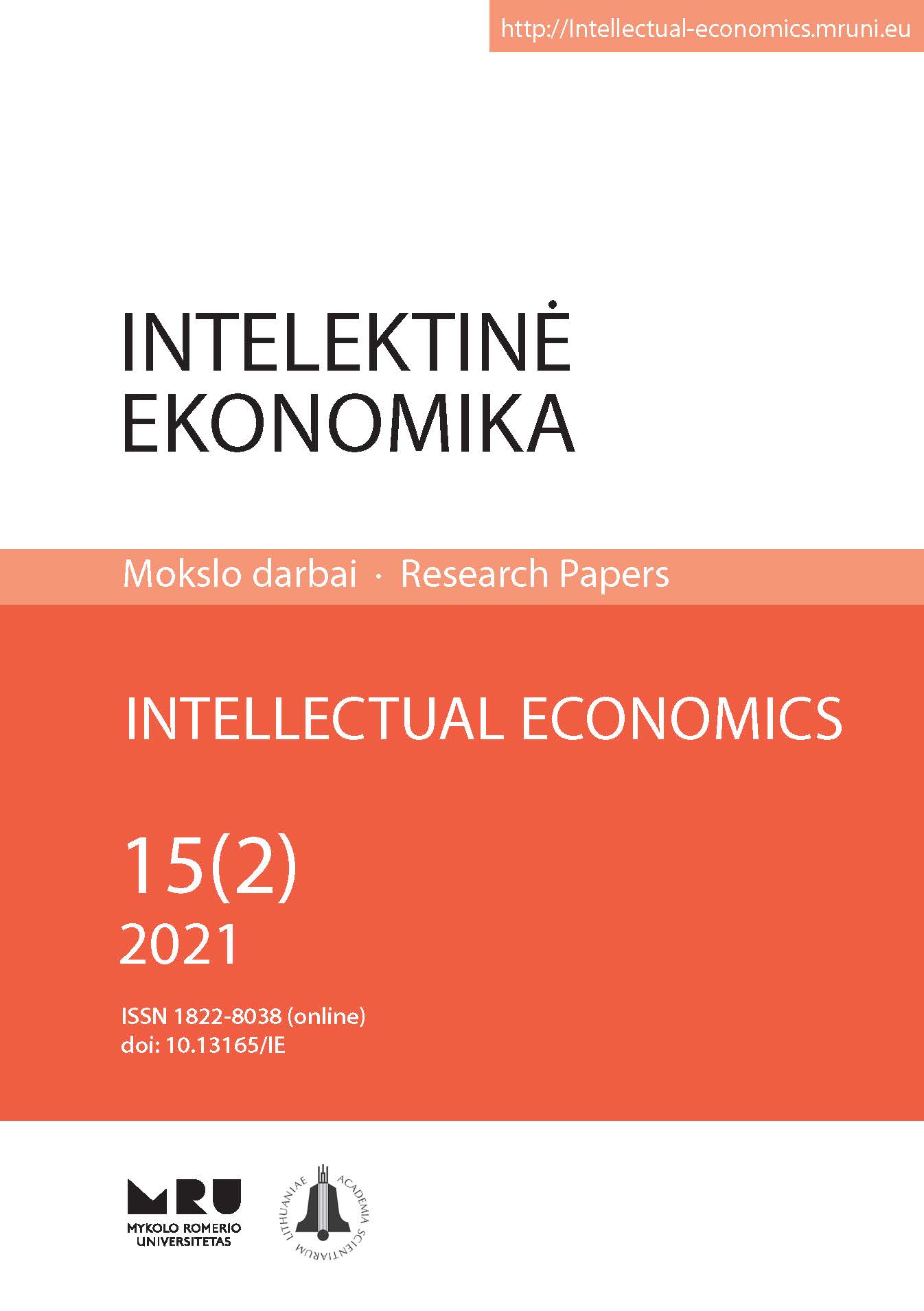
Best practices for supplier diversity
Incorporating a supplier diversity program can be a daunting task. It can be hard to implement but diverse suppliers can help your business. Here are three tips that will help you effectively implement a supplier variety program. First, identify a diverse supplier pool. Ask your existing vendors to recommend diverse vendors. WBENC chapters are another great source for diverse suppliers.
Define clear goals. These goals should be achievable and quantifiable. One example of a goal might be to add 2 new suppliers each year. One goal might be to have every RFP include a requirement that diverse bids are allowed. These goals should be communicated to all employees and tracked throughout the year.
Customer sentiment is leading to higher interest in supplier diversity
Companies are increasing their supplier diversity initiatives to improve customer sentiment. Coca-Cola Company for example has pledged to spend $500 Million with Black-owned Suppliers by 2020, double its previous commitment. These actions show a growing commitment of large companies towards supplier diversity. The trend is likely to continue, as more consumers are demanding more diverse suppliers.
Supplier diversity programs help companies meet their moral obligations by allowing them to work with a broader range of suppliers, while maintaining high ethical standards. UPS, for example, launched a supplier diversity program in 1992, and today, the company spends $2.6 billion annually with diverse suppliers, with plans to increase this amount year-over-year.
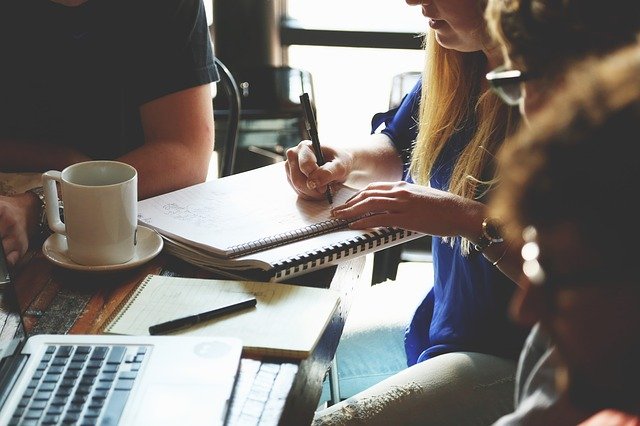
Important importance of supplier diversity within the organization
Traditionally, suppliers have been biased towards manufacturing, distribution and management functions. The challenge that organizations face is finding ways to broaden their supplier diversity beyond their existing base. Organizations can improve their chances of attracting diverse suppliers and increase their financial impact by retooling business strategies.
Diverse suppliers help reduce costs, innovate, and build trust between consumers. In addition, they attract top talent to work for the company. Coca-Cola found that consumers trust the brand more when it is inclusive of diverse suppliers. This led to higher brand trust, and consequently, increased sales. Target, Walmart, and other companies have made supplier diversity a top priority.
FAQ
What is Six Sigma?
It's an approach to quality improvement that emphasizes customer service and continuous learning. The objective is to eliminate all defects through statistical methods.
Motorola developed Six Sigma in 1986 to help improve its manufacturing processes.
The idea spread quickly in the industry. Today many organizations use six-sigma techniques to improve product design.
How do we build a culture that is successful in our company?
A culture of respect and value within a company is key to a productive culture.
It's founded on three principal principles:
-
Everybody has something of value to share
-
People are treated fairly
-
Individuals and groups can have mutual respect
These values can be seen in the behavior of people. They will treat others with kindness and consideration.
They will listen respectfully to the opinions of others.
They encourage others to express their feelings and ideas.
Company culture also encourages open communication, collaboration, and cooperation.
People feel comfortable expressing their opinions freely without fear of reprisal.
They understand that mistakes can be forgiven as long as they're dealt with honestly.
Finally, the company culture promotes honesty and integrity.
Everyone understands that the truth is always best.
Everyone is aware that rules and regulations apply to them.
People don't expect special treatment or favors.
What is Kaizen, exactly?
Kaizen is a Japanese term meaning "continuous improvement." It is a philosophy that encourages employees to constantly look for ways to improve their work environment.
Kaizen is built on the belief that everyone should be able do their jobs well.
How does Six Sigma work?
Six Sigma uses statistical analysis for problems to be found, measured, analyzed root causes, corrected, and learned from.
The first step is to identify the problem.
Next, data is collected and analyzed to identify trends and patterns.
The problem can then be fixed by taking corrective measures.
The data are then reanalyzed to see if the problem is solved.
This continues until the problem has been solved.
What are some of the common mistakes made by managers?
Sometimes, managers make their job more difficult than it is.
They may not assign enough responsibilities to staff members and provide them with inadequate support.
Managers often lack the communication skills necessary to motivate and guide their teams.
Managers sometimes set unrealistic expectations of their teams.
Some managers may try to solve every problem themselves instead of delegating responsibility to others.
What is the difference in leadership and management?
Leadership is about being a leader. Management is about controlling others.
A leader inspires others while a manager directs them.
Leaders inspire people to achieve success. Managers keep their workers focused.
A leader develops people; a manager manages people.
What is the difference between Six Sigma Six Sigma and TQM?
The main difference between these two quality-management tools is that six-sigma concentrates on eliminating defects while total QM (TQM), focuses upon improving processes and reducing expenses.
Six Sigma is an approach for continuous improvement. This method emphasizes eliminating defects using statistical methods such p-charts, control charts, and Pareto analysis.
This method attempts to reduce variations in product output. This is achieved by identifying and addressing the root causes of problems.
Total Quality Management involves monitoring and measuring every aspect of the organization. Training employees is also part of total quality management.
It is used to increase productivity.
Statistics
- Our program is 100% engineered for your success. (online.uc.edu)
- As of 2020, personal bankers or tellers make an average of $32,620 per year, according to the BLS. (wgu.edu)
- 100% of the courses are offered online, and no campus visits are required — a big time-saver for you. (online.uc.edu)
- UpCounsel accepts only the top 5 percent of lawyers on its site. (upcounsel.com)
- The average salary for financial advisors in 2021 is around $60,000 per year, with the top 10% of the profession making more than $111,000 per year. (wgu.edu)
External Links
How To
How can you create a Quality Management Plan, (QMP)?
QMP, which was introduced by ISO 9001:2008, is a systematic approach to improving products, services, and processes through continuous improvement. It provides a systematic approach to improving processes, products and customer satisfaction by continuously measuring, analysing, controlling, controlling, and improving them.
QMP is a common method to ensure business performance. QMP improves production, service delivery, as well as customer relations. QMPs should address all three dimensions: Products, Services, and processes. If the QMP focuses on one aspect, it is called "Process." QMP. When the QMP focuses on a Product/Service, it is known as a "Product" QMP. The QMP that focuses on customer relationships is known as the "Customer" QMP.
When implementing a QMP, there are two main elements: Scope and Strategy. These elements are as follows:
Scope: This determines the scope and duration of the QMP. For example, if you want to implement a QMP that lasts six months, then this scope will outline the activities done during the first six.
Strategy: This describes how you will achieve the goals in your scope.
A typical QMP is composed of five phases: Planning Design, Development, Implementation and Maintenance. Here are the details for each phase.
Planning: In this stage, the objectives of the QMP are identified and prioritized. All stakeholders involved in the project are consulted to understand their requirements and expectations. The next step is to create the strategy for achieving those objectives.
Design: This stage is where the design team creates the vision, mission and strategies necessary for successful implementation of QMP. These strategies are then put into practice by creating detailed plans.
Development: Here the development team works toward building the necessary resources and capabilities to support the successful implementation.
Implementation: This refers to the actual implementation or the use of the strategies planned.
Maintenance: The maintenance of the QMP is an ongoing task.
The QMP must also include several other items:
Participation of Stakeholders: The QMP's success depends on the participation of stakeholders. They need to be actively involved in the planning, design, development, implementation, and maintenance stages of the QMP.
Initiation of a Project: A clear understanding and application of the problem statement is crucial for initiating a project. In other words, they must understand the motivation for initiating the project and the expectations of the outcome.
Time frame: The QMP's timeframe is critical. A simple version is fine if you only plan to use the QMP for a brief period. However, if you have a long-term commitment, you may require more elaborate versions.
Cost Estimation: Another important component of the QMP is cost estimation. Planning is not possible without knowing the amount of money you will spend. It is therefore important to calculate the cost before you start the QMP.
QMPs should not be considered a static document. It is constantly changing as the company changes. It should be reviewed on a regular basis to ensure that it is still meeting the company's needs.