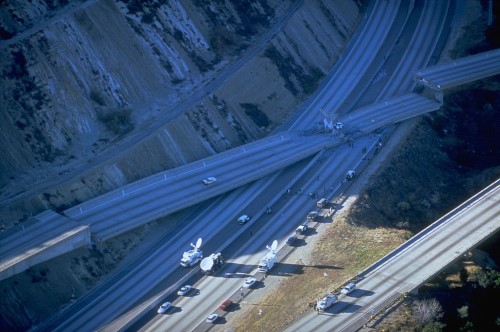
You need to get a degree that is focused on supply chain management if you wish to pursue a career. You can take on the role of leader in a business by earning a degree in supply chain management. It includes strategic, tactical and operational levels. This helps to improve organizational performance. This requires communication skills.
Project management is one form of supply chain management
Supply chain management, which is essential for any business, is important. Project management can help improve the management of your supply chain. Project management helps you create and implement a business plan. A project's main objective is to deliver a finished product that meets all the criteria and goals. The project manager is responsible for ensuring that products and/or services are delivered in a timely manner and that they meet the quality standards. Project management offers many benefits, such as improved collaboration, cost-savings and quality control. There are also some drawbacks to project management.
Although tactics and strategy are important, they should not be implemented without proper planning. A strategy that is not well-planned can lead to a project going sour and resulting in failure to meet its goals. The process of project management is crucial to successful implementation of a supply chain project. Project managers can use best practices to implement solutions and create new strategies to meet current needs.
It encompasses tactical, operational, and strategic levels.
A supply chain can be divided into three major levels - strategic, tactical, and operational. The strategic level is crucial to supply chain success, as it sets the groundwork for all other levels. It involves collecting and analysing data, evaluating the major factors that affect the supply chain, and making decisions based on that information. While operational decisions may be taken to satisfy customer needs, strategic ones are essential for the overall success in the supply chain.
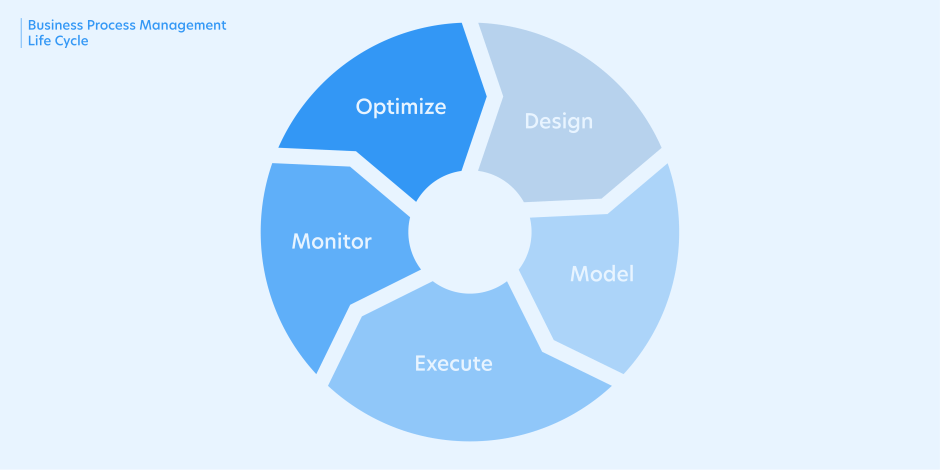
The strategic level describes the company's goals and strengths, as well as identifies weaknesses and formulates a vision for its future. Tactical level involves executing plans that achieve the strategy, with specific measures to meet them. These plans could include invoicing, inventory management (production scheduling), shipping and forecasting. However, some analysts argue that the globalization and resulting in purely strategic functions has made tactical planning less important.
It increases organizational performance
An organization's ability and capacity to improve its supply-chain management performance is key to its effectiveness. There are many ways to measure and evaluate supply chain performance, including customer relationship management (CRM), intra-supply chain management (ISC) and information sharing. These methods can all be used to improve organizational performance.
Supply chains are not all created equal. Some companies have never created a coherent supply chain structure. This results in single functions reporting to different parent functions, or even different points within a parent function. This creates confusion and can slow down response times to urgent problems. For example, demand planning processes may report to the supply-chain lead in one geography, but to sales leads in another. Companies can experience inefficiencies due to these organizational problems.
Communication skills are required.
Supply chain management requires strong communication skills. Supply chain leaders must be able to convey complex ideas and foster collaboration. They should also be able create precise reports. These skills can help you improve your career prospects. Consider furthering your education to get certified in supply chain management.
As a supply chain manager, you will interact with many different people. You will need to be able to listen and empathize with others. Without empathy, your leadership may be rejected, particularly during periods of change. If you don't listen to your employees, they may feel undervalued or rejected. As a result, it is essential to learn more about yourself and develop your skills.
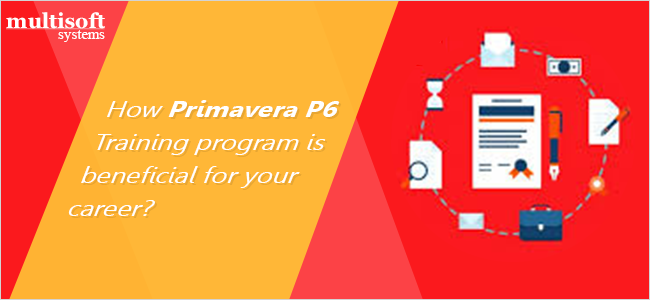
It could lead to a career within supply chain management
A degree in supply management could open doors to many career options. Supply chain managers are responsible for managing a range of processes from forecasting consumer demand, to the delivery of finished products on shelves. This job requires the management of a complex network of vendors and people. To be successful, supply chain managers need to be proficient in both business management and computer science.
The supply chain management degree can be done online or in an actual classroom setting. The training you receive will be the same as a four-year degree program. While online programs are less likely to offer networking opportunities, they provide comparable quality training. Strong analytical skills and a passion to work with data and forecasts are essential. An online degree program can help you teach technical aspects of supply chain administration to others.
FAQ
What is Six Sigma?
It's a strategy for quality improvement that emphasizes customer care and continuous learning. The objective is to eliminate all defects through statistical methods.
Motorola developed Six Sigma in 1986 to help improve its manufacturing processes.
The idea quickly spread in the industry. Many organizations today use six-sigma methods to improve product design and production, delivery and customer service.
What is a simple management tool that aids in decision-making and decision making?
A decision matrix is an easy but powerful tool to aid managers in making informed decisions. It allows them to consider all possible solutions.
A decision matrix represents alternatives in rows and columns. This allows you to easily see how each choice affects others.
This example shows four options, each represented by the boxes on either side of the matrix. Each box represents an option. The top row shows the status quo (the current situation), and the bottom row shows what would happen if nothing was done at all.
The middle column shows the effect of choosing Option 1. It would increase sales by $2 million to 3 million in this instance.
The effects of options 2 and 3 are shown in the next columns. These positive changes can increase sales by $1 million or $500,000. These changes can also have negative effects. For instance, Option 2 increases cost by $100 thousand while Option 3 reduces profits by $200 thousand.
Finally, the last column shows the results of choosing Option 4. This results in a decrease of sales by $1,000,000
The best part about using a decision matrix to guide you is that you don’t need to keep track of which numbers go where. Simply look at the cells to instantly determine if one choice is better than the other.
This is because your matrix has already done the hard work. Simply compare the numbers within the cells.
Here's a sample of how you might use decision matrixes in your business.
You want to decide whether or not to invest more money into advertising. This will allow you to increase your revenue by $5000 per month. But, you will also incur additional expenses of $10 thousand per month.
Look at the cell immediately below the one that states "Advertising" to calculate the net investment in advertising. It's $15,000. Advertising is more valuable than its costs.
What are some common mistakes managers make?
Sometimes, managers make their job more difficult than it is.
They may not delegate enough responsibilities and not provide sufficient support.
A majority of managers lack the communication skills needed to motivate their team and lead them.
Some managers set unrealistic expectations for their staff.
Some managers may try to solve every problem themselves instead of delegating responsibility to others.
What are the 5 management processes?
Each business has five stages: planning, execution and monitoring.
Planning is about setting goals for your future. It includes defining what you want to achieve and how you plan to do it.
Execution is the actual execution of the plans. These plans must be adhered to by everyone.
Monitoring is the process of evaluating your progress toward achieving your objectives. Regular reviews of performance against targets, budgets, and other goals should be part.
At the end of every year, reviews take place. They are a chance to see if everything went smoothly during the year. If not then, you can make changes to improve your performance next year.
After the annual review is complete, evaluations are conducted. It helps to determine what worked and what didn’t. It also provides feedback on the performance of people.
What are the most important management skills?
Management skills are essential for any business owner, whether they're running a small local store or an international corporation. These skills include the ability manage people, finances and resources as well as other factors.
When you need to manage people, set goals, lead teams, motivate them, solve problems, develop policies and procedures and manage change, management skills are essential.
As you can see, there are many managerial responsibilities!
Statistics
- As of 2020, personal bankers or tellers make an average of $32,620 per year, according to the BLS. (wgu.edu)
- This field is expected to grow about 7% by 2028, a bit faster than the national average for job growth. (wgu.edu)
- Your choice in Step 5 may very likely be the same or similar to the alternative you placed at the top of your list at the end of Step 4. (umassd.edu)
- Hire the top business lawyers and save up to 60% on legal fees (upcounsel.com)
- 100% of the courses are offered online, and no campus visits are required — a big time-saver for you. (online.uc.edu)
External Links
How To
How does Lean Manufacturing work?
Lean Manufacturing methods are used to reduce waste through structured processes. They were created by Toyota Motor Corporation in Japan in the 1980s. It was designed to produce high-quality products at lower prices while maintaining their quality. Lean manufacturing seeks to eliminate unnecessary steps and activities in the production process. It is made up of five elements: continuous improvement, continuous improvement, just in-time, continuous change, and 5S. It is a system that produces only the product the customer requests without additional work. Continuous improvement is constantly improving upon existing processes. Just-in-time is when components and other materials are delivered at their destination in a timely manner. Kaizen means continuous improvement, which is achieved by implementing small changes continuously. Five-S stands for sort. It is also the acronym for shine, standardize (standardize), and sustain. These five elements work together to produce the best results.
The Lean Production System
Six key concepts are the basis of lean production:
-
Flow is about moving material and information as near as customers can.
-
Value stream mapping is the ability to divide a process into smaller tasks, and then create a flowchart that shows the entire process.
-
Five S's, Sort, Set in Order, Shine. Standardize. and Sustain.
-
Kanban – visual signals like colored tape, stickers or other visual cues are used to keep track inventory.
-
Theory of Constraints - Identify bottlenecks in the process, and eliminate them using lean tools such kanban boards.
-
Just-in Time - Send components and material directly to the point-of-use;
-
Continuous improvement is making incremental improvements to your process, rather than trying to overhaul it all at once.