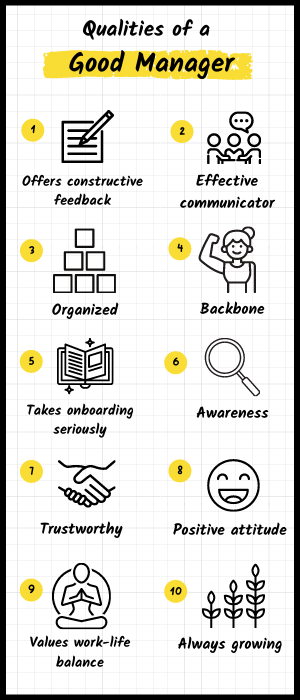
CSCMP stands to Certified Systems and Communications Manager and is an important certification for communications and systems professionals. CSCMP exam has 160 questions. It takes about four hours to complete. Pearson VUE is an independent third-party company that administers the exam. There are many testing centers around the world. The test is proctored on the spot and confers pass/fail status.
Academic membership
Academic membership in CSCM is open to academics who hold full-time positions at accredited colleges or universities. The annual membership fee is $175. It provides you with the opportunity to join collaborative forums and help develop course content. Members can also network with colleagues in the field. Contact us if you're interested in joining the CSCM.
Cost of membership
The Council of Supply Chain Management Professionals is an organization dedicated to connecting, educating, and developing supply chain professionals around the globe. The group is $149 and you will have six months access to all the benefits and events that the organization offers. A six-month membership is also available for $88 for young professionals. Both membership options expire August 31, 2021.
CSCMP membership grants you access to many resources including surveys and research. Members have access to the most recent research and valuable insights. Members can also access webinars that are completely free. CSCMP membership can help you learn more about supply-chain management and how to improve business operations.
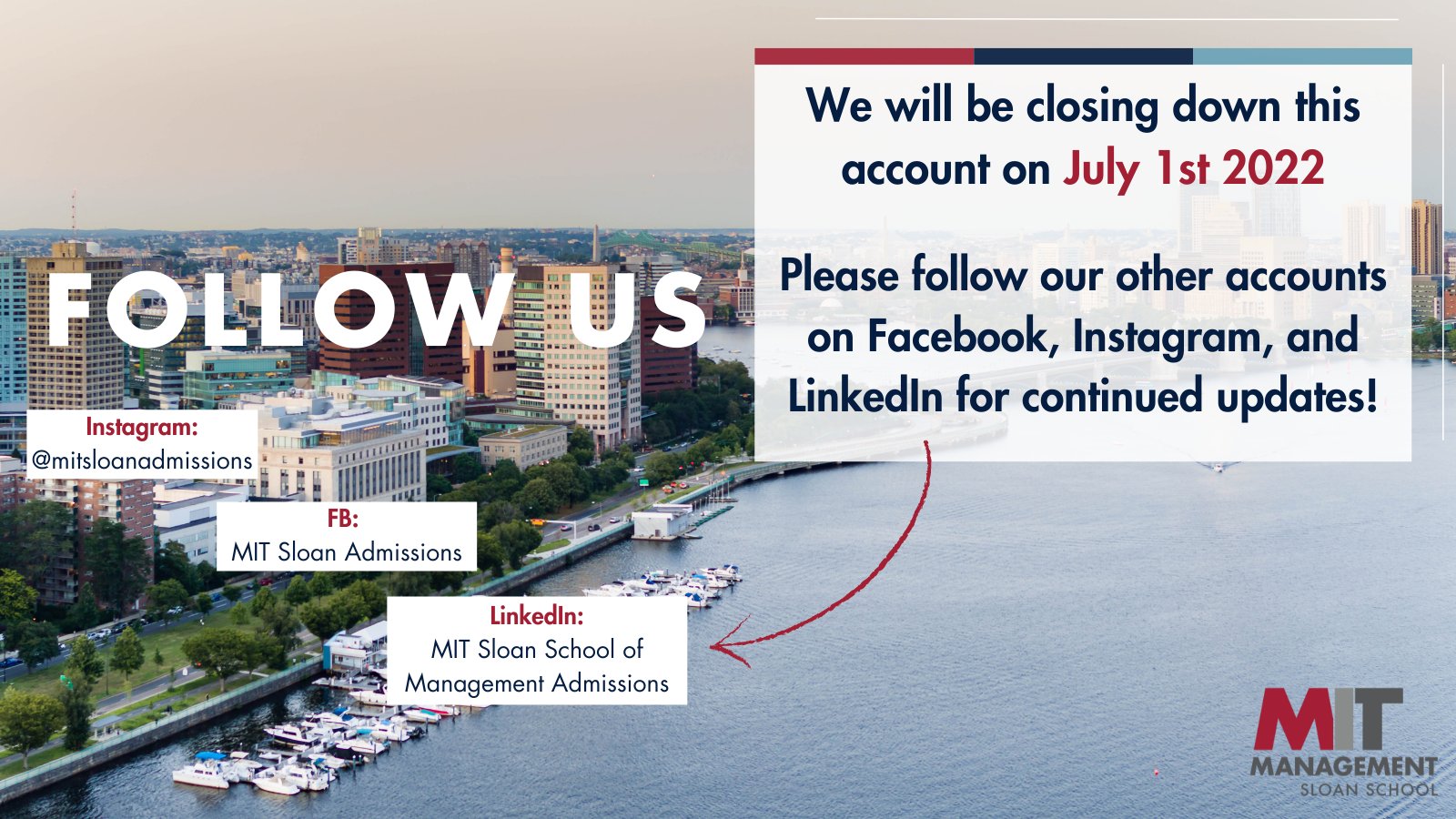
You can become a CSCMP member by taking the SCMP level two exam. You can take the exam within one year of submitting your membership fee. You will be sent a confirmation email a week or so prior to your scheduled test date.
FAQ
How do we build a culture that is successful in our company?
A positive company culture creates a sense of belonging and respect in its people.
It is founded on three basic principles:
-
Everybody has something to offer.
-
People are treated fairly
-
It is possible to have mutual respect between groups and individuals
These values are evident in the way that people act. They will treat others with consideration and courtesy.
They will listen respectfully to the opinions of others.
They will also encourage others to share their ideas and feelings.
The company culture promotes collaboration and open communication.
People are free to speak out without fear of reprisal.
They know that they will not be judged if they make mistakes, as long as the matter is dealt with honestly.
Finally, the company culture encourages honesty as well as integrity.
Everybody knows they have to tell the truth.
Everyone recognizes that rules and regulations are important to follow.
People don't expect special treatment or favors.
What are the 3 main management styles?
There are three main management styles: participative, laissez-faire and authoritarian. Each style is unique and has its strengths as well as weaknesses. Which style do yo prefer? Why?
Autoritarian – The leader sets the direction for everyone and expects them to follow. This style is best when the organization has a large and stable workforce.
Laissez-faire: The leader lets each person decide for themselves. This approach works best in small, dynamic organizations.
Participative - The leader listens to ideas and suggestions from everyone. This is a great style for smaller organizations that value everyone.
What is Six Sigma?
It's an approach to quality improvement that emphasizes customer service and continuous learning. The objective is to eliminate all defects through statistical methods.
Motorola created Six Sigma as part of their efforts to improve manufacturing processes in 1986.
This idea quickly spread throughout the industry. Today, many organizations use six sigma methods for product design, production and delivery.
What can a manager do to improve his/her management skillset?
It is important to have good management skills.
Managers must continuously monitor the performance levels of their subordinates.
You should immediately take action if you see that your subordinate is not performing as well as you would like.
You should be able pinpoint what needs to improve and how to fix it.
What are your main management skills
No matter if they are running a local business or an international one, management skills are vital. They are the ability to manage people and finances, space, money, and other factors.
When you need to manage people, set goals, lead teams, motivate them, solve problems, develop policies and procedures and manage change, management skills are essential.
As you can see there is no end to the number of managerial tasks.
What are management concepts?
Management Concepts are the principles and practices managers use to manage people and resources. They cover topics like job descriptions (job descriptions), performance evaluations, training programmes, employee motivation and compensation systems.
Statistics
- Our program is 100% engineered for your success. (online.uc.edu)
- The BLS says that financial services jobs like banking are expected to grow 4% by 2030, about as fast as the national average. (wgu.edu)
- 100% of the courses are offered online, and no campus visits are required — a big time-saver for you. (online.uc.edu)
- Hire the top business lawyers and save up to 60% on legal fees (upcounsel.com)
- As of 2020, personal bankers or tellers make an average of $32,620 per year, according to the BLS. (wgu.edu)
External Links
How To
How do I do the Kaizen Method?
Kaizen means continuous improvement. Kaizen is a Japanese concept that encourages constant improvement by small incremental changes. It's a team effort to continuously improve processes.
Kaizen is one method that Lean Manufacturing uses to its greatest advantage. The concept involves employees responsible for manufacturing identifying problems and trying to fix them before they become serious issues. This is how you can improve the quality and lower the cost.
The main idea behind kaizen is to make every worker aware of what happens around him/her. Correct any errors immediately to avoid future problems. If someone spots a problem while at work, they should immediately report it to their manager.
Kaizen has a set of basic principles that we all follow. We always start from the end product and move toward the beginning. We can improve the factory by first fixing the machines that make it. Next, we fix the machines which produce components. Then we fix the workers, who directly work with these machines.
This approach is called 'kaizen' because it focuses on improving everything steps by step. After we're done with the factory, it's time to go back and fix the problem.
It is important to understand how to measure the effectiveness and implementation of kaizen in your company. There are many methods to assess if kaizen works well. Another method is to see how many defects are found on the products. Another way is to see how much productivity has increased since implementing kaizen.
A good way to determine whether kaizen has been implemented is to ask why. Did you do it because it was legal or to save money? Did you really think that it would help you achieve success?
Congratulations! Now you're ready for kaizen.