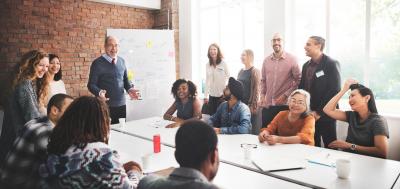
IT financial management involves the control and strategic planning of a company's financial activities. It is concerned with the profitability of a business, its expenses, and its cash and credit flows. Its goal is to protect the financial interests of investors and ensure that business growth can be achieved. This article will give a brief overview of IT financial control. Here are a few examples.
IT financial management refers to the planning, organization, direction, and control of financial activities for a company.
The key to running a business is financial management. It's about managing a company’s finances. It also helps to plan its future. It includes decisions regarding capital investment, profit distribution, and liabilities. These decisions will determine how a company allocates its money to achieve its goals. The financial manager is also responsible for ensuring that the company meets its tax obligations.
Financial management is often about how a company pays for its day to day operations and expansion. A company could raise funds through private equity investment, sell assets, and issue stock. But before pursuing these options, a company must have enough cash to cover its day-to-day expenses and purchase raw materials. The company may also want to introduce new products that require additional investment. A financial manager needs to evaluate the cost and determine the best source for financing it.
Strategic planning is what a business should do to earn and spend more money.
Financial management's goal is to help business owners figure out how to pay the costs of running their businesses. This includes making decisions regarding raising capital, borrowing money, and creating and sticking to a budget. The process includes analyzing data and determining how to improve the business. This begins with the recording of all income and expenses. Accounting prepares the financial reports for businesses, such as balance sheets, cash flow statements, profit and losses statements, budgets and balance sheet.
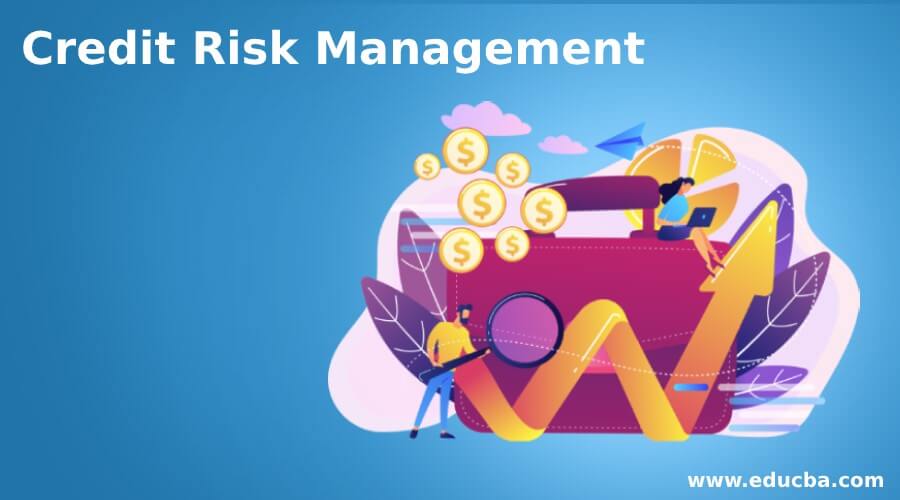
FAQ
What is the difference of leadership and management?
Leadership is about inspiring others. Management is about controlling others.
A leader inspires his followers while a manager directs the workers.
Leaders motivate people to succeed; managers keep workers on track.
A leader develops people; a manager manages people.
What are the 3 main management styles?
These are the three most common management styles: participative (authoritarian), laissez-faire (leavez-faire), and authoritarian. Each style has strengths and flaws. Which style do YOU prefer? Why?
Autoritarian – The leader sets the direction for everyone and expects them to follow. This style works best if the organization is large and stable.
Laissez-faire - The leader allows each individual to decide for him/herself. This style is most effective when the organization's size and dynamics are small.
Participative: The leader listens to everyone's ideas and suggestions. This style is best for small organizations where everyone feels valued.
How do you define Six Sigma?
Six-sigma will be well-known to anyone who has worked in operations research or statistics. Anyone involved in business can benefit.
Because it requires a high degree of commitment, only leaders with strong leadership skills can implement it successfully.
What are management concepts, you ask?
Management Concepts are the management principles and practices that managers use in managing people and resources. They cover topics such as job descriptions and performance evaluations, human resource policies, training programs, employee motivation, compens systems, organizational structure, among others.
What is Six Sigma and how can it help you?
This is a method of quality improvement that emphasizes customer service, continuous learning, and customer service. It is a method that eliminates defects using statistical techniques.
Six Sigma was developed at Motorola in 1986 as part of its efforts to improve manufacturing processes.
It was quickly adopted by the industry and many companies are now using six-sigma to improve product design, production, delivery, customer service, and product design.
What are the main management skills?
Managerial skills are crucial for every business owner, regardless of whether they run a small store in their locality or a large corporation. These include the ability and willingness to manage people, finances as well resources, time and space.
Managerial skills are required when setting goals and objectives and planning strategies, leading employees, motivating them, solving problems, creating policies, procedures, or managing change.
There are so many managerial tasks!
What is Kaizen?
Kaizen is a Japanese term which means "continuous improvement." This philosophy encourages employees to continually look for ways to improve the work environment.
Kaizen is based upon the belief that each person should be capable of doing his or her job well.
Statistics
- The BLS says that financial services jobs like banking are expected to grow 4% by 2030, about as fast as the national average. (wgu.edu)
- Our program is 100% engineered for your success. (online.uc.edu)
- Your choice in Step 5 may very likely be the same or similar to the alternative you placed at the top of your list at the end of Step 4. (umassd.edu)
- As of 2020, personal bankers or tellers make an average of $32,620 per year, according to the BLS. (wgu.edu)
- This field is expected to grow about 7% by 2028, a bit faster than the national average for job growth. (wgu.edu)
External Links
How To
What is Lean Manufacturing?
Lean Manufacturing methods are used to reduce waste through structured processes. They were developed in Japan by Toyota Motor Corporation (in the 1980s). The aim was to produce better quality products at lower costs. Lean manufacturing is about eliminating redundant steps and activities from the manufacturing process. It has five components: continuous improvement and pull systems; just-in time; continuous change; and kaizen (continuous innovation). Pull systems are able to produce exactly what the customer requires without extra work. Continuous improvement means continuously improving on existing processes. Just-in–time refers when components or materials are delivered immediately to their intended destination. Kaizen is continuous improvement. This can be achieved by making small, incremental changes every day. Finally, 5S stands for sort, set in order, shine, standardize, and sustain. These five elements are combined to give you the best possible results.
Lean Production System
Six key concepts make up the lean manufacturing system.
-
Flow - The focus is on moving information and material as close as possible to customers.
-
Value stream mapping- This allows you to break down each step of a process and create a flowchart detailing the entire process.
-
Five S's: Sort, Shine Standardize, Sustain, Set In Order, Shine and Shine
-
Kanban - visual cues such as stickers or colored tape can be used to track inventory.
-
Theory of constraints: Identify bottlenecks and use lean tools such as kanban boards to eliminate them.
-
Just-in-time delivery - Deliver components and materials right to your point of use.
-
Continuous improvement - Make incremental improvements rather than overhauling the entire process.