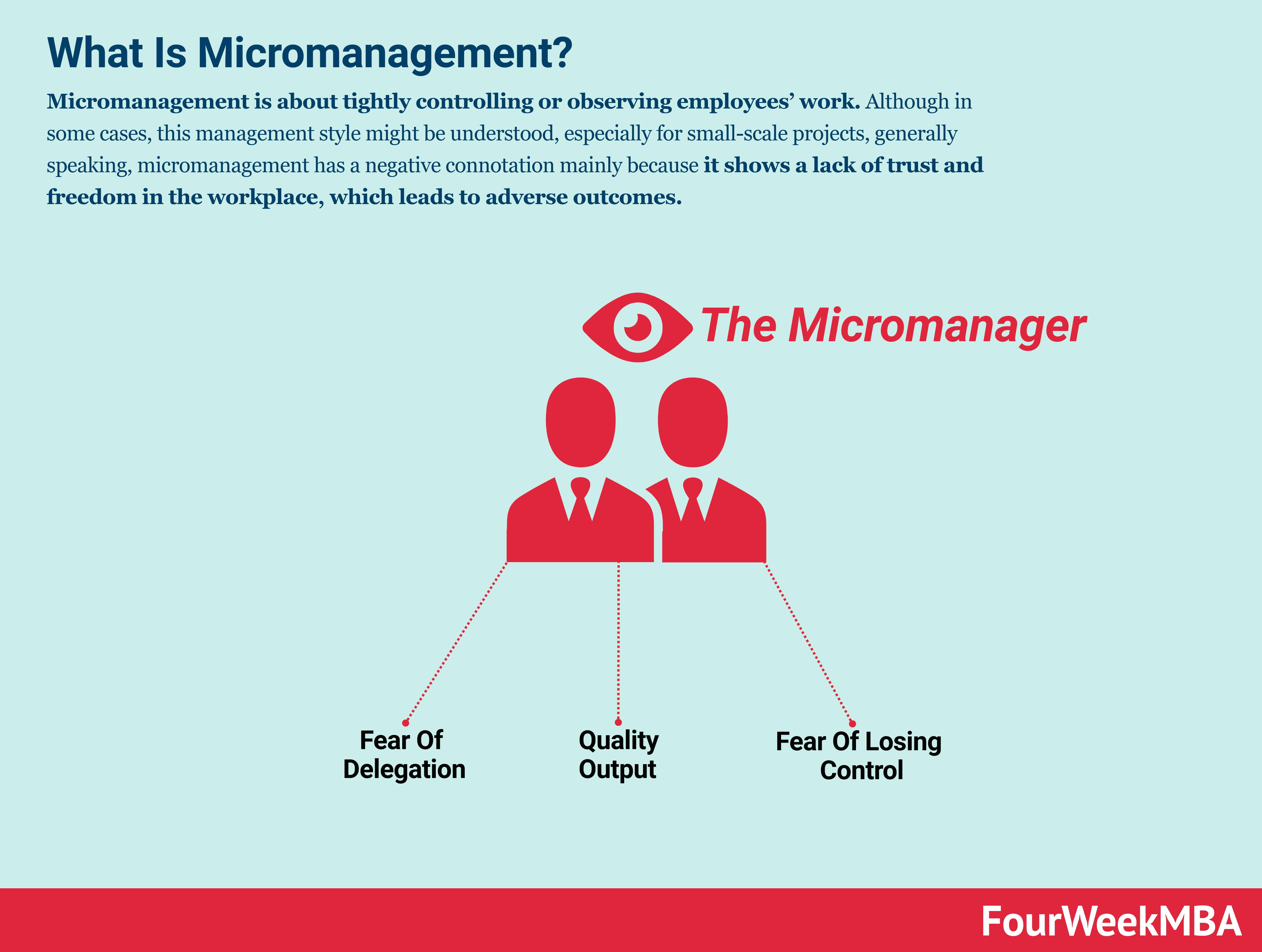
When creating a capacity planning strategy, you need to consider the expected growth of the workload, including any customer-driven growth and new features. Plan accordingly. Here are four common scenarios to consider: Lead, Lag, Match, Adjustment. Each scenario offers different benefits and challenges. Each scenario has its own benefits and challenges. You need to carefully consider each one in order for your capacity planning to be effective.
Lead strategy
Companies that have a leading strategy for capacity planning take an active role in increasing capacity and expanding the system before there is a demand. The other strategy is a lag strategy that waits for the demand to grow before expanding capacity. A lead strategy has the advantage that it doesn't run out of capacity in case of an unexpected rise in demand.
This strategy can be used in many circumstances, but it is most useful when the volume or quality of goods or service will be greater than expected. It can also help when demand rises quickly, such as during the holidays. If a retailer hires seasonal workers in the holiday season, it can improve its workforce for greater traffic. A lead strategy also allows for quick additions of headcount.
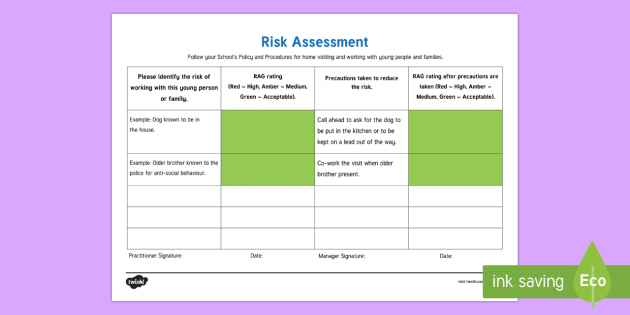
Lag strategy
The Lag strategy for capacity planning is used to match capacity to demand. Although this strategy is less risky that the Lead strategy, it takes a lot more effort and work. It is also less risk-averse compared to the other strategies. The lead strategy on the other side tries to predict future demand, and then expand capacity accordingly. This strategy might not work for all organizations because of time constraints or resource limitations.
A lag strategy is a good choice for companies with a stable business model. It helps to avoid wasteful production and excess inventory. This method increases the stress of recruiting and training new employees. A lead strategy, by contrast, is more aggressive. This strategy anticipates future needs and meets them prior to they occur.
Match strategy
The Match strategy serves as a compromise between the Lead- and Lag strategies. This strategy emphasizes incremental capacity increases, and not boosting demand ahead. While it requires more planning and implementation work, it is the safer bet for most manufacturers. The decision to increase capacity is not cheap, but it will be less risky than the other two strategies.
Match strategy includes monitoring current demand and forecast analysis. This allows the company's ability to quickly adapt to changes. This strategy is more labor intensive, but allows for quick pivots. It also helps streamline operations by ensuring that the resources available are adequate for the current and future demands.
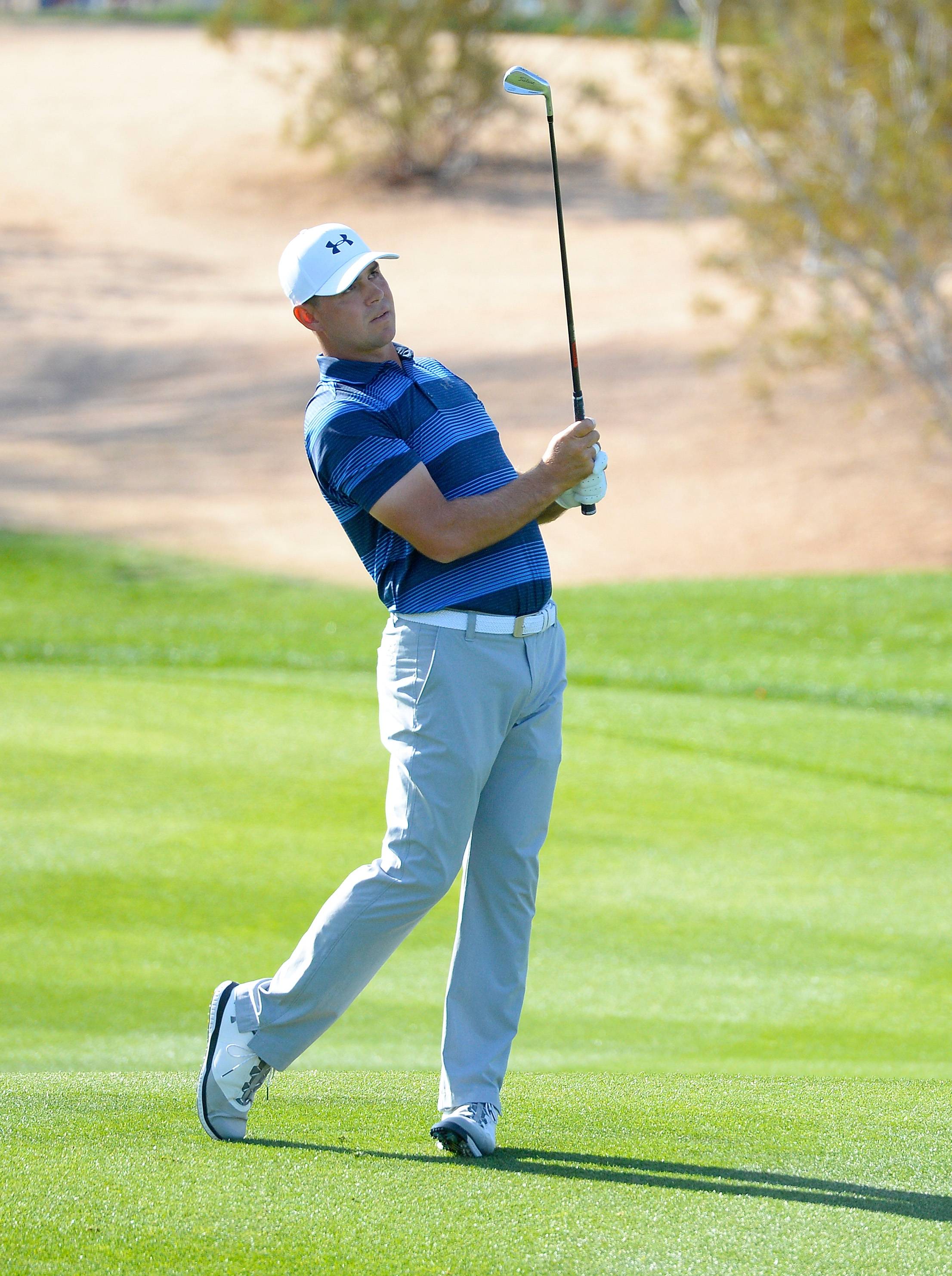
Adjustment strategy
The common approach to managing supply chain capacities is called the Adjustment strategy. This ensures that the supply network is always ready to respond to demand. It helps businesses to meet their deadlines and scale up their businesses. The right strategy will increase your bottom line. The Adjustment strategy can be used to help companies meet their supply-chain demands more efficiently.
It forces organizations and workers to be more realistic about their resource allocations. Overestimating resources can cause low productivity and low employee morale. Over-allocating funds can create significant opportunity costs. They could have been spent improving service, innovation, and employee pay. This strategy makes it more difficult for leaders to forecast their budgets realistically.
FAQ
Why is it so important for companies that they use project management techniques
Project management techniques are used in order to ensure projects run smoothly, and that deadlines are met.
This is because many businesses depend heavily upon project work to produce products and services.
These projects must be managed efficiently and effectively by companies.
Companies may lose their reputation, time and money if they do not have effective project management.
What role can a manager fill in a company’s management?
Different industries have different roles for managers.
Managers generally oversee the day-today operations of a business.
He/she ensures that the company meets its financial obligations and produces goods or services that customers want.
He/she makes sure that employees adhere to the rules and regulations as well as quality standards.
He/she oversees marketing campaigns and plans new products.
How can a manager enhance his/her leadership skills?
Through demonstrating good management skills at every opportunity
Managers must continuously monitor the performance levels of their subordinates.
It is important to take immediate action if your subordinate doesn't perform as expected.
You should be able pinpoint what needs to improve and how to fix it.
What is TQM?
The industrial revolution saw the realization that prices alone were not sufficient to sustain manufacturing companies. This led to the birth of quality. To remain competitive, they had to improve quality as well as efficiency.
Management developed Total Quality Management to address the need for improvement. It focused on all aspects of an organisation's performance. It included continual improvement processes, employee involvement, customer satisfaction, and customer satisfaction.
Statistics
- The BLS says that financial services jobs like banking are expected to grow 4% by 2030, about as fast as the national average. (wgu.edu)
- 100% of the courses are offered online, and no campus visits are required — a big time-saver for you. (online.uc.edu)
- Hire the top business lawyers and save up to 60% on legal fees (upcounsel.com)
- As of 2020, personal bankers or tellers make an average of $32,620 per year, according to the BLS. (wgu.edu)
- Our program is 100% engineered for your success. (online.uc.edu)
External Links
How To
How do I get my Six Sigma certification?
Six Sigma can be used to improve quality and efficiency. It's a methodology that helps companies achieve consistent results from their operations. The name comes from the first two letters of the Greek word "sigmas" which mean "six." Motorola developed this process in 1986. Motorola recognized the need to standardize manufacturing processes in order to produce better products at a lower cost. They had been having problems with consistency because of the many different people who were doing the work. They used statistical tools such as Pareto analysis, control charts, and Pareto analysis to resolve the problem. Then, they would apply these techniques in every area of the operation. They would then be able make improvements where needed. Three main steps are involved when you're trying to go through the whole process of getting your Six Sigma certification. The first step is to find out if you're qualified. You'll want to take some classes and pass them before you start taking any tests. After passing the classes, you will be able to take the tests. You will want to remember everything you learned in the class. Once you have completed the class, you will be ready for the test. If you pass, you'll get certified. Finally, you can add your certifications on to your resume.