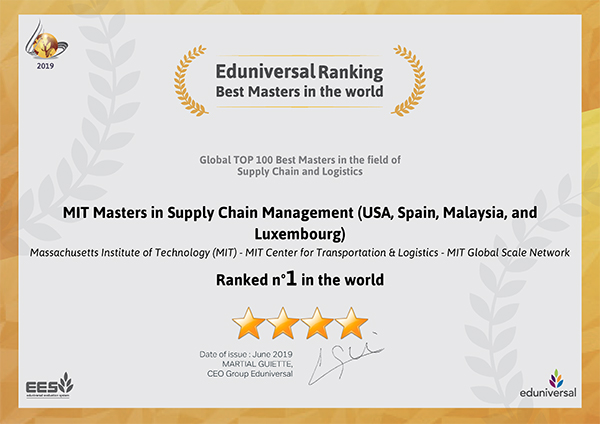
A continuous improvement methodology can be used to achieve desired results over time. This type of methodology consists of iterative processes over several design generations. This is also known by Lean Six Sigma. This article will be discussing one variation on the PDSA procedure based SIPOC analysis. Its application is discussed in the context of an engineering design studio.
Lean Six Sigma
Lean Six Sigma (or Continuous Improvement) is a methodology that helps to make processes simpler and more predictable. Simpler processes result in fewer errors, thus lowering the risk of process failures. The methodology uses statistical process control (SPC) techniques to control process variables and improve performance. This method can be used for improving any product or process. The company must set measurable parameters and use data as a guide to make changes.
PDSA
The PDSA continuous improvement method uses a continuous loop that includes process design, analysis, action, and monitoring to improve a company's business processes. The study step in PDSA's initial phase is where the team evaluates and compares the results of an experiment. This step allows the team and the client to evaluate whether the improvement was a significant success. This step will allow the team to conduct analysis. They may use control charts to distinguish expected from special cause variation.
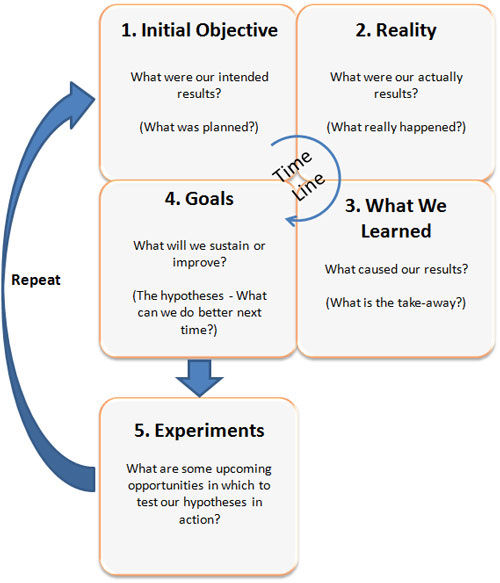
Variation of PDSA
PDSA (Personal Development and Support) is a method of continuous improvement and problem-solving, with a clearly defined focus and measurable targets. The process begins with careful planning. Next, it moves to taking effective action. Next, each idea must be tested and evaluated for feasibility and viability. Project team members measure the results to ensure that every change leads to lasting improvements.
PDSA based SIPOC Analysis
SIPOC analysis provides a powerful tool for optimizing business processes. It's an easy way to categorize data into five categories. SIPOC diagrams can help teams better understand their processes by providing a high-level overview of each. They are also a great way to focus discussions.
PDSA based DMAIC
Organizations looking to improve their processes can use continuous improvement methods that follow DMAIC. These methods are structured and straightforward, and they are designed to help organizations understand and eliminate ineffective processes while achieving measurable and sustainable results. These tools can help organizations track which changes have the most impact and which ones are not. They may also have difficulty implementing effective controls.
PDSA based in kanban board
Kanban boards are a great tool. You can visualize the work in progress and assign tasks to team members. Attachments or images can also be added to each task. They also allow you to control the amount of work that is completed and when it is finished.
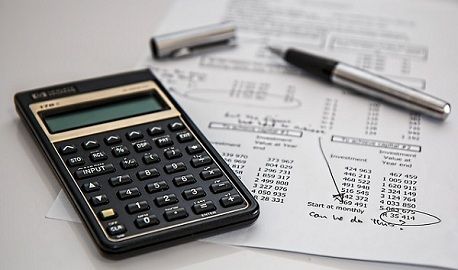
Kaizen based SIPOC Analysis
The SIPOC structure is a powerful tool for improving process performance. It is used to define the boundaries of a process and gather pertinent information. Then, it presents that information in an easy-to-understand manner. It is useful in the Define phase, which is part of DMAIC methodologies, to identify process variations and key performance indicator (KVIPs) that can affect KVIPs. It is also useful for teams and other stakeholders to plan improvements to improve processes.
PDSA based PDSA variation
Continuous improvement methodology PDSA uses the principle of continuous comparison between actual and expected results. The PDSA methodology measures the actual results of an improvement project against the expected outcomes. Then the reality of implementation is compared with that plan. The team then analyses the data to determine if there were any measurable improvements. The team often uses a control chart to distinguish between expected variation or special cause variation.
FAQ
How can we make our company culture successful?
A successful company culture is one that makes people feel valued and respected.
It's founded on three principal principles:
-
Everybody can contribute something valuable
-
Fair treatment of people is the goal
-
People and groups should respect each other.
These values reflect in how people behave. They will treat others with respect and kindness.
They will respect other people's opinions.
They encourage others to express their feelings and ideas.
Additionally, the company culture encourages open communication as well as collaboration.
People feel safe to voice their opinions without fear of reprisal.
They are aware that mistakes can be accepted if they are treated honestly.
The company culture promotes honesty, integrity, and fairness.
Everyone is aware that truth must be told.
Everyone understands there are rules that they must follow.
Nobody expects to be treated differently or given favors.
Why is it important for companies to use project management techniques?
Project management techniques are used in order to ensure projects run smoothly, and that deadlines are met.
This is due to the fact that most businesses rely heavily upon project work in order to produce goods, and services.
These projects must be managed efficiently and effectively by companies.
Companies may lose their reputation, time and money if they do not have effective project management.
What is a management tool to help with decision-making?
The decision matrix is a powerful tool that managers can use to help them make decisions. They can think about all options and make informed decisions.
A decision matrix is a way of representing alternatives as rows and columns. This makes it easy to see how each alternative affects other choices.
In this example, we have four possible alternatives represented by the boxes on the left side of the matrix. Each box represents a different option. The top row represents the current state of affairs, and the bottom row is indicative of what would happen in the event that nothing were done.
The middle column displays the impact of selecting Option 1. It would translate into an increase in sales from $2million to $3million.
The following columns illustrate the impact of Options 2 and 3. These are good changes, they increase sales by $1million or $500,000. These changes can also have negative effects. Option 2 increases the cost of goods by $100,000. Option 3 decreases profits and makes them less attractive by $200,000.
The final column shows results of choosing Option 4. This results in a decrease of sales by $1,000,000
The best part of using a decision-matrix is that it doesn't require you to know which numbers belong where. You can just glance at the cells and see immediately if one given choice is better.
The matrix has already done all of the work. Simply compare the numbers within the cells.
Here's an example showing how you might use a Decision Matrix in your business.
It is up to you to decide whether to spend more money on advertising. If you do this, you will be able to increase revenue by $5000 per month. But, you will also incur additional expenses of $10 thousand per month.
By looking at the cell just below "Advertising", the net result can be calculated as $15 thousand. Advertising is worth much more than the investment cost.
What are the key management skills?
Any business owner needs to be able to manage people, finances, resources and time. They are the ability to manage people and finances, space, money, and other factors.
Managerial skills are required when setting goals and objectives and planning strategies, leading employees, motivating them, solving problems, creating policies, procedures, or managing change.
As you can see there is no end to the number of managerial tasks.
Statistics
- Hire the top business lawyers and save up to 60% on legal fees (upcounsel.com)
- UpCounsel accepts only the top 5 percent of lawyers on its site. (upcounsel.com)
- As of 2020, personal bankers or tellers make an average of $32,620 per year, according to the BLS. (wgu.edu)
- 100% of the courses are offered online, and no campus visits are required — a big time-saver for you. (online.uc.edu)
- This field is expected to grow about 7% by 2028, a bit faster than the national average for job growth. (wgu.edu)
External Links
How To
How can you implement the Kaizen technique?
Kaizen means continuous improvement. The term was coined in the 1950s at Toyota Motor Corporation and refers to the Japanese philosophy emphasizing constant improvement through small incremental changes. It's a process where people work together to improve their processes continuously.
Kaizen is one the most important methods of Lean Manufacturing. In this concept, employees who are responsible for the production line must identify problems that exist during the manufacturing process and try to solve them before they become big issues. This improves the quality of products, while reducing the cost.
Kaizen is about making everyone aware of the world around them. So that there is no problem, you should immediately correct it if something goes wrong. If someone is aware of a problem at work, he/she should inform his/her manager immediately.
Kaizen is based on a few principles. Start with the end product, and then move to the beginning. For example, if we want to improve our factory, we first fix the machines that produce the final product. Then, we fix the machines that produce components and then the ones that produce raw materials. Then we fix the workers, who directly work with these machines.
This method, called 'kaizen', focuses on improving each and every step of the process. Once the factory is fixed, we return to the original site and work our way back until we get there.
To implement kaizen in your business, you need to find out how to measure its effectiveness. There are many methods to assess if kaizen works well. Another way to determine if kaizen is working well is to look at the quality of the products. Another way to find out how productive your company has been since you implemented kaizen is to measure the increase in productivity.
Another way to know whether kaizen is working is to ask yourself why did you decide to implement kaizen. Did you do it because it was legal or to save money? Did you really believe it would lead to success?
Congratulations! You're ready to start kaizen.