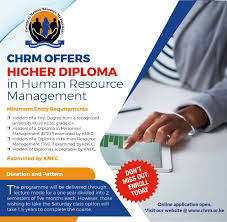
This method is suitable for projects that are simple and have a tight schedule. To resolve site-related problems and achieve project goals, the project team must work together early. The owners must also communicate with the contractor and architect. In addition, they must trust and be clear about their expectations. If an owner is unsure, he can consult a project manager to explain the process.
IPD
IPD's project delivery model helps to build trust among team members and foster collaboration in order for them to achieve common goals. It helps define project goals and risks for all project participants, promoting the ownership of the project and equality of the playing field among team members. It reduces rework by keeping project participants updated on progress.
An IPD team, which is composed of key project participants, is established by the project owner. Teamwork is encouraged by the fact that incentives are tied to project milestones and goals. The performance of participants also affects the compensation. This aligns their financial interests, making project costs predictable and affordable.
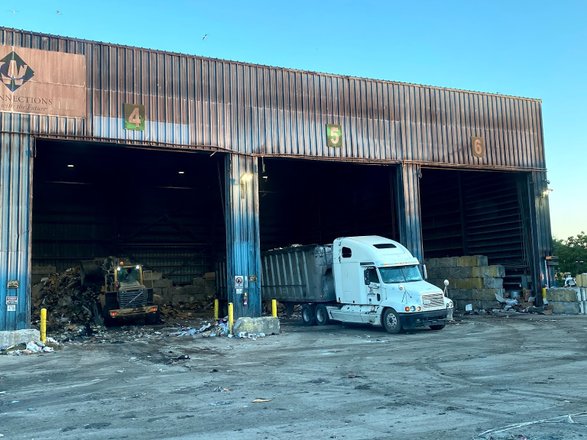
Design-Build
Design-Build is an excellent option for many construction projects. This allows the owner to be involved in the design and planning phases of the project. This early collaboration helps to avoid potential conflicts between contractor and owner. It results in lower construction cost and a faster schedule. A design-build contractor is able to work without the involvement of an in-house manager. This frees up the owner's time to focus on the design elements of the project.
In the contract documents, it is important to clearly state the scope of work in a Design/Build project. The design-builder should be paid for their work in the early stages. The contract should also outline the frequency of design submittals and the processes for review of these submissions.
Construction manager at risk
The construction manager at-risk (CMA at risk) delivery method is unique in that design as well as construction are separately contracted. The construction manager in this method is chosen based on more factors than the total construction cost. The CM at Risk is responsible for delivering projects to owner specifications and within a specified maximum price. The construction manager is also a consultant for the project owner during the design phase and as the general contractor during construction.
One of the primary advantages of this approach is the reduction of risk for all parties. This method of project delivery is not suitable for all projects. The construction manager at the risk is not an engineer or contractor, as Design-Build and BidBuild are different. The construction manager must have high visibility to all project stakeholders. To avoid payment delays, the project manager must adhere to the guaranteed maximum cost.
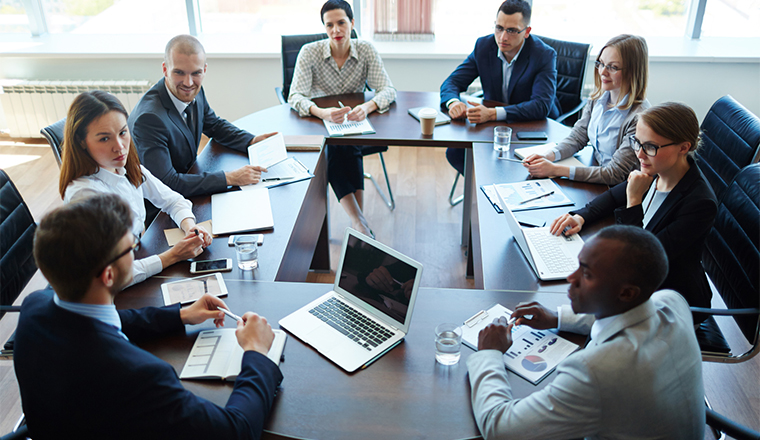
Integrated project delivery
All project stakeholders are involved in an integrated project delivery (IDP), from design to management. This method allows stakeholders to take a more holistic view of the project. It is beneficial for all. The process also eliminates waiting periods between construction phases, which improves productivity. Participating early in the project can improve decision-making by sharing the knowledge of all team members. Additionally, this approach makes the most of technological advancements.
Companies can use an integrated project delivery system to address any challenges encountered during construction. To help identify the problem and take action, the Deming Cycle template can also be used by construction teams if they are unable to finish projects on time. The IPD process is a way to foster collaboration among stakeholders and help them work toward a common goal.
FAQ
What role does a manager have in a company's success?
There are many roles that a manager can play in different industries.
In general, a manager controls the day-to-day operations of a company.
He/she will ensure that the company fulfills its financial obligations.
He/she ensures that employees follow the rules and regulations and adhere to quality standards.
He/she is responsible for the development of new products and services, as well as overseeing marketing campaigns.
What are some common management mistakes?
Managers can make their jobs more difficult than necessary.
They might not give enough support and delegate the right responsibilities to their staff.
Additionally, many managers lack communication skills that are necessary to motivate and direct their teams.
Managers can set unrealistic expectations for their employees.
Some managers may try to solve every problem themselves instead of delegating responsibility to others.
How can a manager motivate employees?
Motivation refers to the desire or need to succeed.
It is possible to be motivated by doing something you enjoy.
You can also feel motivated by making a positive contribution to the success in the organization.
For example, if you want to become a doctor, you'll probably find it more motivating to see patients than to study medicine books all day.
Motivation comes from within.
One example is a strong sense that you are responsible for helping others.
You might even enjoy the work.
If you don’t feel motivated, find out why.
Then think about how you can make your life more motivating.
What is TQM, exactly?
The industrial revolution saw the realization that prices alone were not sufficient to sustain manufacturing companies. This led to the birth of quality. They needed to improve quality and efficiency if they were going to remain competitive.
Management realized the need to improve and created Total Quality Management, which focused on improving all aspects within an organization's performance. It included continuous improvement and employee involvement as well as customer satisfaction.
What are the 3 basic management styles?
There are three main management styles: participative, laissez-faire and authoritarian. Each style has its strengths and weaknesses. Which style do your prefer? Why?
Authoritarian - The leader sets the direction and expects everyone to comply with it. This style works best if the organization is large and stable.
Laissez faire - Each individual can decide for himself/herself. This approach works best in small, dynamic organizations.
Participative - The leader listens to ideas and suggestions from everyone. This style works best in smaller organizations where everyone feels valued.
What is the difference between leadership and management?
Leadership is about inspiring others. Management is about controlling others.
Leaders inspire others, managers direct them.
A leader motivates people and keeps them on task.
A leader develops people; a manager manages people.
Statistics
- UpCounsel accepts only the top 5 percent of lawyers on its site. (upcounsel.com)
- Your choice in Step 5 may very likely be the same or similar to the alternative you placed at the top of your list at the end of Step 4. (umassd.edu)
- This field is expected to grow about 7% by 2028, a bit faster than the national average for job growth. (wgu.edu)
- The profession is expected to grow 7% by 2028, a bit faster than the national average. (wgu.edu)
- The BLS says that financial services jobs like banking are expected to grow 4% by 2030, about as fast as the national average. (wgu.edu)
External Links
How To
How can you use the Kaizen method?
Kaizen means continuous improvement. The Japanese philosophy emphasizes small, incremental improvements to achieve continuous improvement. This term was created by Toyota Motor Corporation in 1950. It's where people work together in order to improve their processes constantly.
Kaizen is one method that Lean Manufacturing uses to its greatest advantage. The concept involves employees responsible for manufacturing identifying problems and trying to fix them before they become serious issues. This will increase the quality and decrease the cost of the products.
Kaizen is an approach to making every worker aware and alert to what is happening around them. If something is wrong, it should be corrected immediately so that no problem occurs. Report any problem you see at work to your manager.
Kaizen is based on a few principles. We always start from the end product and move toward the beginning. We can improve the factory by first fixing the machines that make it. Next, we fix the machines which produce components. Finally, we repair the workers who are directly involved with these machines.
This method, called 'kaizen', focuses on improving each and every step of the process. After we're done with the factory, it's time to go back and fix the problem.
To implement kaizen in your business, you need to find out how to measure its effectiveness. There are several ways that you can tell if your kaizen system is working. One method is to inspect the finished products for defects. Another way is to check how much productivity has grown since kaizen was implemented.
You can also find out if kaizen works by asking yourself why you decided to implement it. It was because of the law, or simply because you wanted to save some money. Did you really believe that it would be a success factor?
Congratulations! Now you're ready for kaizen.