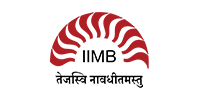
Talent supply chain management aims to increase the supply of talent as well as the services provided by talent. A company can achieve its strategic goals by improving its ability to produce, distribute and deliver talent. Continue reading to learn more about this proactive approach in talent management. In this article, we will explore how this approach can improve your company's human capital management and production processes. We will also discuss how this approach can reduce the risks associated contingent workers.
Supply chain for adaptive talent
It is crucial to develop an adaptive talent chain in order to attract and retain the best talent. This process can help to balance your workforce as well as meet changing business requirements. Employers face constant challenges to adapt to changing workforce demographics, shortages of smart skills, and other obstacles that can hinder their ability to remain competitive. These are just a few ways you can implement an adaptive talent supply system in your company. The first step is to identify your talent gaps.
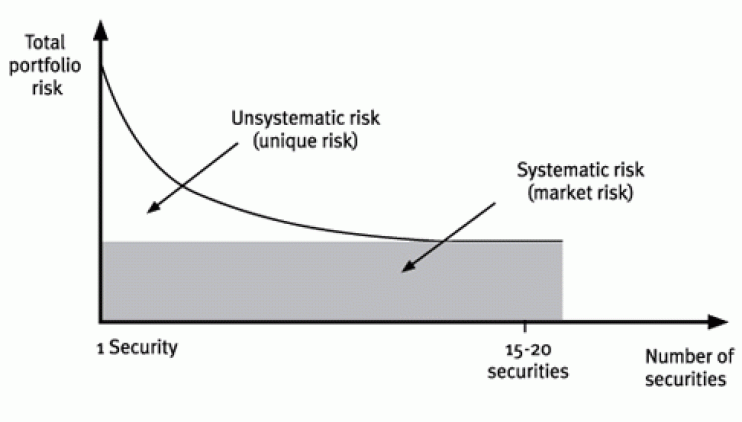
Developing existing talent
A vital part of any organization's success is developing existing talent. There are many ways to develop talent. Supply chain success requires that companies continue to grow their talent, as well as finding and nurturing the best professionals. This requires collaboration between human resources and the supply chain functions. The development of existing talent is a key step in the talent management system, but it can be challenging.
Recruiting new talent
Employers have difficulty finding qualified candidates due to the increasing difficulty in finding workers. While some people attribute the Great Resignation to the increased retirement rate and inability to afford childcare, as well as general reevaluation on work, the root problem is structural. One reason for this problem is a lackluster talent supply chain.
Limiting the risk of contingent workers
Although contingent workers offer many advantages, they also pose risks that companies must take into consideration. Employers recognize the benefits, but are not equipped to deal with these risks. Employers need to create an integrated risk management model that addresses all aspects of contingent labor management. This model should cover contracts, audits and other critical aspects necessary for the implementation of a successful contingent workforce management system.
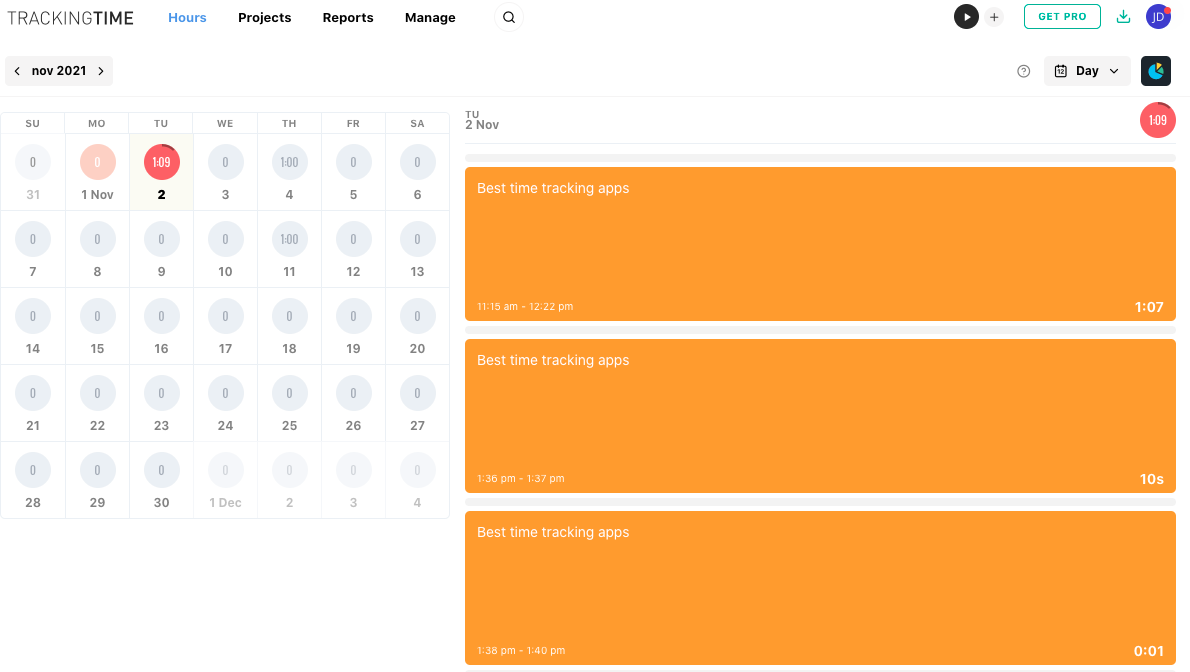
Managing existing talent
Employers' talent strategy should include the development of existing talent. The skills of existing employees are a critical part of a company's competitive advantage. In many cases, however, leaving is the best way to move up in a company. Turnover is high and many businesses struggle to retain existing employees. Investment in the workforce can help to prevent turnover. This is why companies need to invest early on in training their workers.
FAQ
What is Six Sigma and how can it help you?
It's an approach to quality improvement that emphasizes customer service and continuous learning. The objective is to eliminate all defects through statistical methods.
Six Sigma was developed at Motorola in 1986 as part of its efforts to improve manufacturing processes.
The idea quickly spread in the industry. Many organizations today use six-sigma methods to improve product design and production, delivery and customer service.
What are the five management steps?
These five stages are: planning, execution monitoring, review and evaluation.
Planning involves setting goals for the future. This includes setting goals for the future and defining what you want.
Execution occurs when you actually carry out the plans. You need to make sure they're followed by everyone involved.
Monitoring is a way to track progress towards your objectives. Regular reviews of performance against budgets and targets should be part of this process.
Every year, there are reviews. They give you an opportunity to review the year and assess how it went. If not then, you can make changes to improve your performance next year.
Following the annual review, evaluation is done. It helps to determine what worked and what didn’t. It also provides feedback on the performance of people.
What are the 4 main functions of management?
Management is responsible for organizing, managing, directing and controlling people, resources, and other activities. Management also involves setting goals and developing policies.
Management assists an organization in achieving its goals by providing direction, coordination and control, leadership, motivation, supervision and training, as well as evaluation.
The following are the four core functions of management
Planning – Planning involves deciding what needs to happen.
Organizing: Organizing refers to deciding how things should work.
Direction - This is the art of getting people to follow your instructions.
Controlling – Controlling is the process of ensuring that tasks are completed according to plan.
Statistics
- As of 2020, personal bankers or tellers make an average of $32,620 per year, according to the BLS. (wgu.edu)
- This field is expected to grow about 7% by 2028, a bit faster than the national average for job growth. (wgu.edu)
- The average salary for financial advisors in 2021 is around $60,000 per year, with the top 10% of the profession making more than $111,000 per year. (wgu.edu)
- The BLS says that financial services jobs like banking are expected to grow 4% by 2030, about as fast as the national average. (wgu.edu)
- UpCounsel accepts only the top 5 percent of lawyers on its site. (upcounsel.com)
External Links
How To
How can I obtain my Six Sigma license
Six Sigma can be used to improve quality and efficiency. It is a method that enables companies to achieve consistent results with their operations. The name is derived from the Greek word "sigmas", which means "six". Motorola developed this process in 1986. Motorola realized they needed to standardize the manufacturing processes to produce products faster and cheaper. The many people involved in manufacturing had caused problems with consistency. To solve this problem, they decided to use statistical tools such as control charts and Pareto analysis. Then, they would apply these techniques in every area of the operation. After applying the technique, they could make improvements wherever there was potential. Three main steps are involved when you're trying to go through the whole process of getting your Six Sigma certification. Finding out if the certification is available for you is the first step. You'll want to take some classes and pass them before you start taking any tests. Once you pass those classes, the test will begin. You will want to remember everything you learned in the class. You'll then be prepared to take the exam. If you pass, then you will become certified. And finally, you'll be able to add your certifications to your resume.