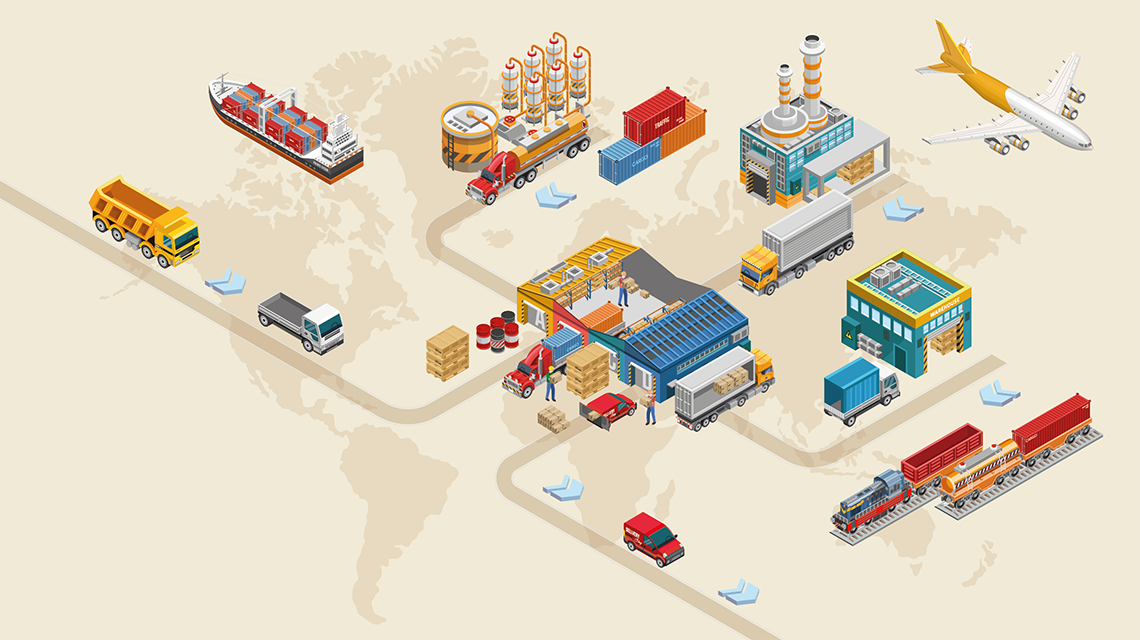
There are four basic management perspectives. These perspectives are Theory. Function. Historical Development. and Future Trends. This article will discuss each of these perspectives. Each perspective has both its benefits and drawbacks. It is important to understand the difference between each perspective. This will allow you to pick the one that best suits you and your preferences. These are just a few examples of management perspectives.
Theories of Management
Management theories are essential in helping to determine the best management strategy for an organisation. Different theories of management focus on different aspects. However, they all relate to management. Although no one theory is right for every organization, it's possible to combine different theories to produce better results. Modern organizations often use a mix of theories which allows for more flexibility in their organizational structures.
Theories of management are used in different settings, from management in general to project management. These theories can be considered condensed knowledge that allows novices to accomplish what experts would do in the context of project management. However, they are most effective when applied in a small project setting, where theory-related issues can be solved without wider penalties. They can cause serious damage to performance and create problems that could be avoided by better management.
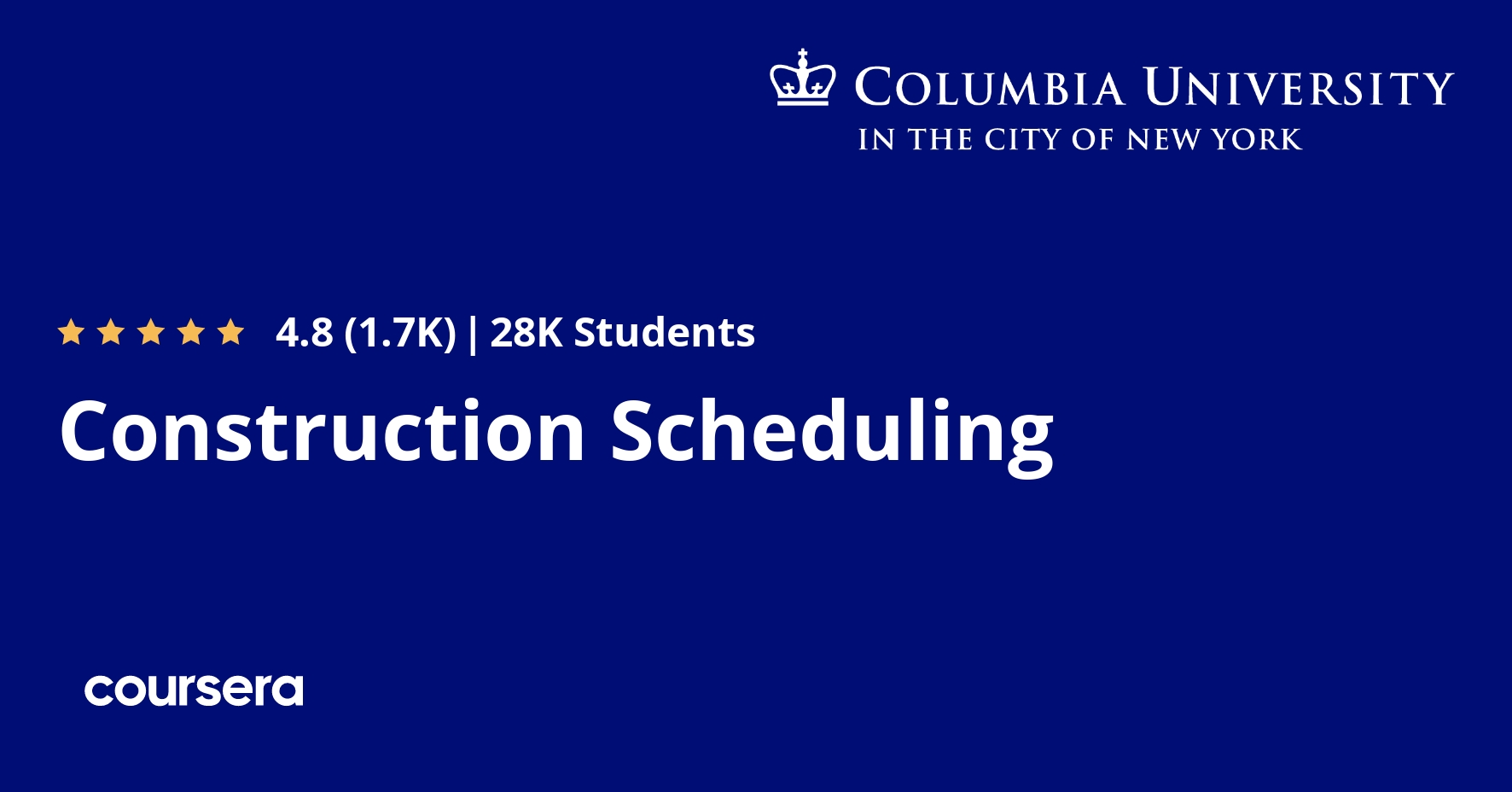
Management functions
For an organisation to succeed, its management functions are essential. They include the following: determining what is required, monitoring performance, and applying corrective steps when necessary. An organization's management plays an important role, especially in achieving its goals regarding profit and market share. Managers must make decisions, set goals, implement strategies and track the progress of various parts of an organization.
Planning is the first step in the managerial process. It involves defining and assessing the goals. This requires an ability to analyze and understand past and current trends as well as the ability develop and implement future strategies. If these functions are carried out properly, an organisation can achieve its goals without experiencing any problems.
Historical development
Management has evolved over the years with new theories that emphasize the human factor. Douglas McGregor's Theory Y, which is a well-known example of this change, is a great example. It also altered the traditional definition of what executives do. They no longer have to be masters of the organisation but can now act more like coaches. The importance of the human element in management and emotional intelligence was rediscovered by organizational theorists.
The Industrial Revolution spurred an intense debate on management theory. This was a crucial moment in management history. Six main management theories were born out of the resulting changes. Each theory is focused on different aspects.
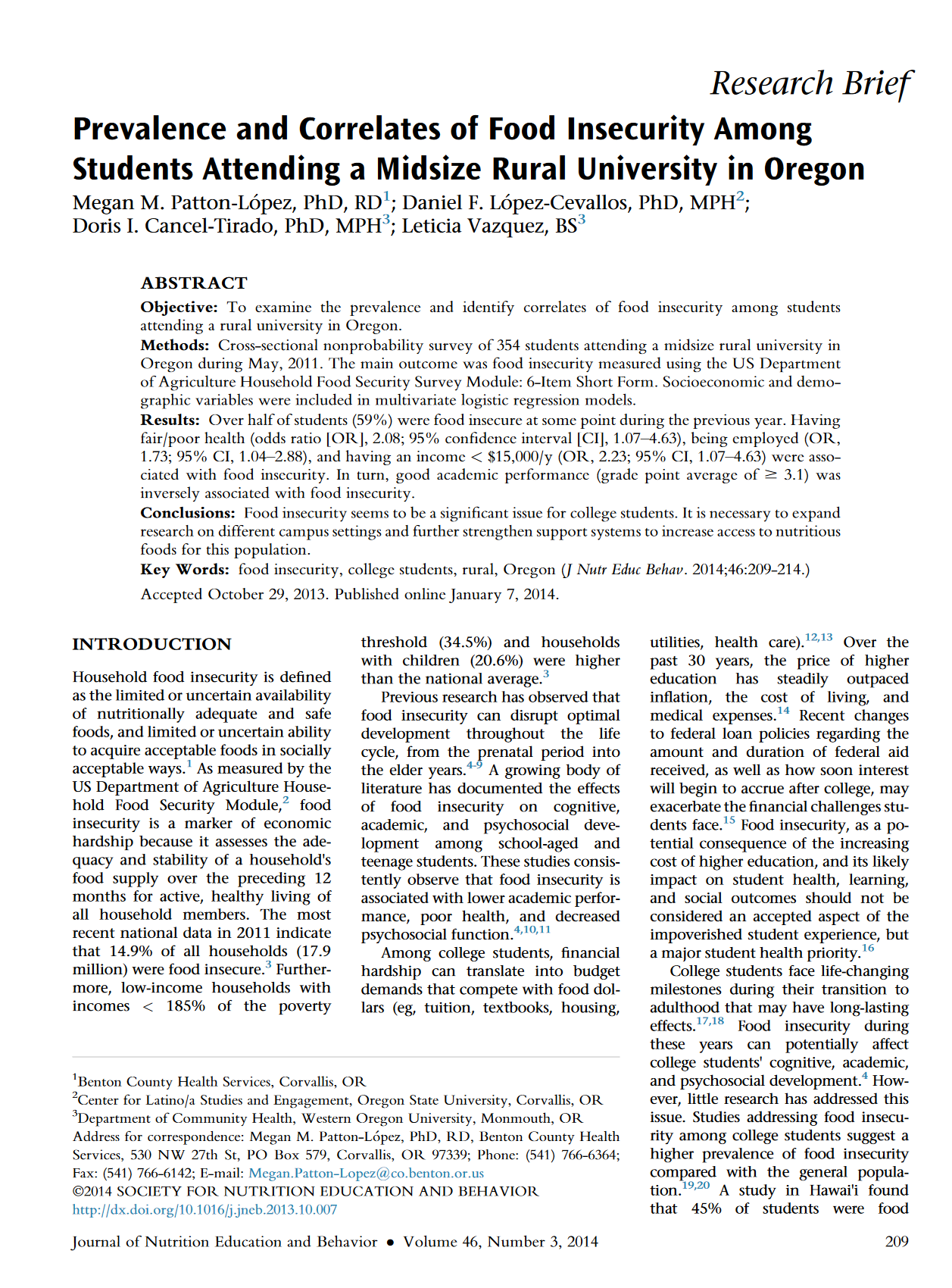
Future trends
A series of trends are shaping the future of management. One of these trends involves the changing role and responsibilities of the manager. This requires managers to be more flexible and agile. Flexibility in work is becoming more standard for managers in the UK. Over half of managers believe flexible working will be the norm within five to ten years. Half also think their direct reports are more flexible than five years ago.
The increasing importance of working relations is one trend that is affecting the sector of management. This trend is being recognized by more than half of managers and they believe it to be a future trend. The emergence of flexible working environments is contributing to this trend. Some people are now more concerned about trust and relationships because of the recent economic downturn. These new trends could help companies retain, develop and attract employees.
FAQ
Six Sigma is so well-known.
Six Sigma is easy and can deliver significant results. Six Sigma provides a framework to measure improvements and allows companies to focus on the most important things.
How does Six Sigma work?
Six Sigma uses statistical analysis to find problems, measure them, analyze root causes, correct problems, and learn from experience.
The first step in solving a problem is to identify it.
The data is then analyzed and collected to identify trends.
The problem is then rectified.
Final analysis of data is done to determine if the problem has been solved.
This cycle continues until there is a solution.
What are the four main functions of management?
Management is responsible of planning, organizing, leading, and controlling people as well as resources. This includes setting goals, developing policies and procedures, and creating procedures.
Management aids an organization in reaching its goals by providing direction and coordination, control, leadership motivation, supervision, training, evaluation, and leadership.
Management has four primary functions:
Planning – Planning involves deciding what needs to happen.
Organizing is the act of deciding how things should go.
Directing - Directing is when you get people to do what you ask.
Controlling - This is the ability to control people and ensure that they do their jobs according to plan.
What is TQM and how can it help you?
The industrial revolution was when companies realized that they couldn't compete on price alone. This is what sparked the quality movement. They needed to improve quality and efficiency if they were going to remain competitive.
To address this need for improvement management created Total Quality Management (TQM) which aimed to improve all aspects of an organization's performance. It included continual improvement processes, employee involvement, customer satisfaction, and customer satisfaction.
Statistics
- The profession is expected to grow 7% by 2028, a bit faster than the national average. (wgu.edu)
- The BLS says that financial services jobs like banking are expected to grow 4% by 2030, about as fast as the national average. (wgu.edu)
- Our program is 100% engineered for your success. (online.uc.edu)
- 100% of the courses are offered online, and no campus visits are required — a big time-saver for you. (online.uc.edu)
- Your choice in Step 5 may very likely be the same or similar to the alternative you placed at the top of your list at the end of Step 4. (umassd.edu)
External Links
How To
How do I do the Kaizen Method?
Kaizen means continuous improvement. This Japanese term refers to the Japanese philosophy of continuous improvement that emphasizes incremental improvements and constant improvement. It is a process where people come together to improve their processes.
Kaizen is one method that Lean Manufacturing uses to its greatest advantage. The concept involves employees responsible for manufacturing identifying problems and trying to fix them before they become serious issues. This increases the quality of products and reduces the cost.
Kaizen is about making everyone aware of the world around them. If something is wrong, it should be corrected immediately so that no problem occurs. It is important that employees report any problems they see while on the job to their managers.
There are some basic principles that we follow when doing kaizen. When working with kaizen, we always start with the end result and move towards the beginning. If we want to improve our factory for example, we start by fixing the machines that make the final product. Next, we fix the machines which produce components. Finally, we repair the workers who are directly involved with these machines.
This is known as "kaizen", because it emphasizes improving each step. We finish fixing the factory and then go back to the beginning. This continues until we achieve perfection.
To implement kaizen in your business, you need to find out how to measure its effectiveness. There are many ways to tell if kaizen is effective. One way is to examine the amount of defects on the final products. Another way is determining how much productivity increased after implementing kaizen.
To determine if kaizen is effective, you should ask yourself why you chose to implement kaizen. Is it because the law required it or because you want to save money. Did you really believe it would lead to success?
Congratulations if you answered "yes" to any of the questions. You're now ready to get started with kaizen.