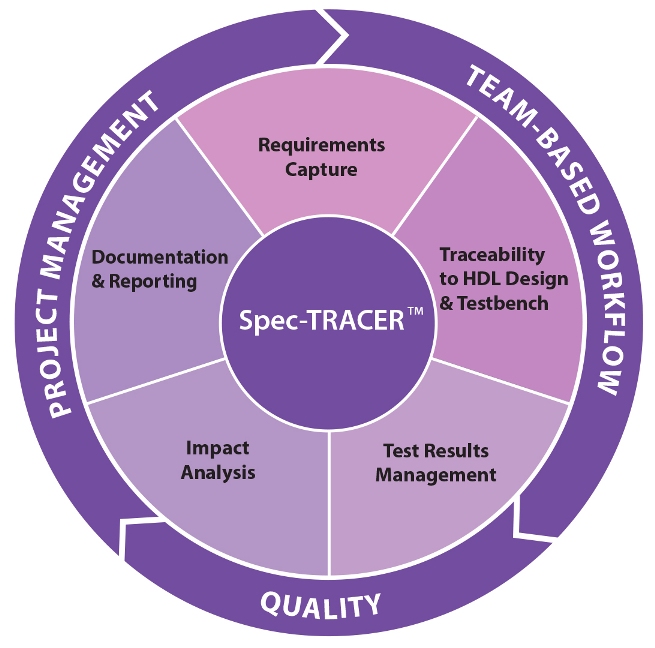
The Associate in Risk Management, (ARM) program teaches students how the rapidly changing world of risks management works. Graduates will be able to manage all aspects risk in their organizations confidently. Learn about operational, financial, and strategic risks while getting a global view. This program was designed with technology-driven perspectives in mind.
ARM designation
An ARM designation can be described as a professional designation in the field of risk management. An ARM designation is a professional designation in risk management. It requires candidates to show competency in risk assessment as well as hazard identification and risk response. For advancement to Fellow Designation of RIMS - a non-profit organization that represents professionals in risk management around the world, an ARM designation will be required.
The ARM program prepares students for rapid technological changes in risk management. With this education, graduates will be able to confidently handle all types of risk in their organizations. They will learn about managing hazard risk and financial risk. Students also get a global perspective of risk management in the program.
Courses
Associate in Risk Management (ARM), courses aim to teach students the rapidly changing field. Students will be able to effectively manage all aspects risk within their organization. Students will learn how to manage operational, financial, and strategic risk. Students are also taught how to manage global risks. This course will give students a technological-driven perspective that will allow them to succeed as a risk manager.

The courses offered by RISK management educational institutions vary. Some of them are designed specifically for risk professionals while others are designed for business generalists. Advanced courses cover strategic risk management. These courses include ethics, governance, reputational risk and internal controls.
Exam
The Associate in Risk Management exam is a professional certification that allows you to be a risk manager. This exam examines quantitative and qualitative risk management techniques and takes into account both the risks and opportunities. This exam helps you to be more aware of risks and make informed decisions. It also helps to learn about risk quadrants as well as their importance.
This certification requires students to complete three core courses and a risk management ethics exam. The exam contains between 15 and forty multiple-choice options. It is graded based on pass/fail. This exam is not for the weak of heart. Keir Educational Ressources has study materials to help you get the Associate in Risk Management certification.
Pay range
According to ZipRecruiter, the average pay range for an associate in risk management is $53,500-$79,500. The highest earners can make as high as $90,000. However, your actual pay range may vary by as much as $25,000 depending on where you live, what employer you work for, and how many years of experience.
The salary ranges for associates working in risk management depend on the location you work in as well as the size and scope of your organization. Larger companies in larger cities will offer higher salaries. You will need a relevant degree from a university, solid knowledge about risk management policies and the ability manage and lead projects.
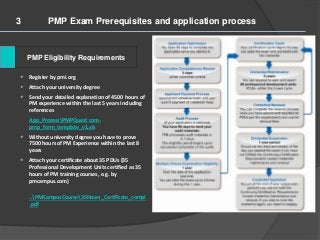
Candidates for ARM receive a free course
The Institutes offers a free course to anyone who wants to become an Associate in Risk Management (ARM). The course will help you prepare for the ARM test. The course is free of charge, and it includes an online module called Ethical Guidelines for Insurance Professionals. Candidates who take the online course can obtain up to 50 credits towards the certification.
The Insurance Institute of America (ARM) has granted the professional designation of Associate in Risk Management. It focuses primarily on the science of risk management. These courses are self study courses and candidates should complete them before taking the exam.
FAQ
What are the three basic management styles?
There are three types of management: participative, laissez faire, and authoritarian. Each style is unique and has its strengths as well as weaknesses. Which style do yo prefer? Why?
Autoritarian – The leader sets the direction for everyone and expects them to follow. This style is best when the organization has a large and stable workforce.
Laissez-faire – The leader gives each individual the freedom to make decisions for themselves. This style is most effective when the organization's size and dynamics are small.
Participative – Leaders are open to suggestions and ideas from everyone. This is a great style for smaller organizations that value everyone.
What are the top management skills?
Management skills are essential for any business owner, whether they're running a small local store or an international corporation. These skills include the ability manage people, finances and resources as well as other factors.
These skills are necessary for setting goals and objectives as well as planning strategies, leading groups, motivating employees and solving problems.
You can see that there are many managerial duties.
How can we create a successful company culture?
A company culture that values and respects its employees is a successful one.
It's based on three main principles:
-
Everyone has something valuable to contribute
-
Fair treatment of people is the goal
-
Individuals and groups can have mutual respect
These values are reflected in the way people behave. They will treat others with respect and kindness.
They will respect other people's opinions.
And they will encourage others to share ideas and feelings.
Company culture also encourages open communication, collaboration, and cooperation.
People feel free to express their views openly without fear of reprisal.
They are aware that mistakes can be accepted if they are treated honestly.
Finally, the company culture promotes honesty and integrity.
Everyone understands that the truth is always best.
Everyone is aware that rules and regulations apply to them.
Nobody expects to be treated differently or given favors.
What are the five management processes?
Planning, execution, monitoring and review are the five stages of any business.
Setting goals for the future requires planning. Planning involves defining your goals and how to get there.
Execution is when you actually execute the plans. You need to make sure they're followed by everyone involved.
Monitoring is a way to track progress towards your objectives. Regular reviews of performance against targets, budgets, and other goals should be part.
Every year, there are reviews. They give you an opportunity to review the year and assess how it went. If not, then it may be possible to make adjustments in order to improve performance next time.
After each year's review, evaluation occurs. It helps identify which aspects worked well and which didn't. It also provides feedback on the performance of people.
What is the difference between management and leadership?
Leadership is about influencing others. Management is about controlling others.
A leader inspires his followers while a manager directs the workers.
A leader motivates people to achieve success; a manager keeps workers on task.
A leader develops people; a manager manages people.
Six Sigma is so popular.
Six Sigma is easy to implement and can produce significant results. Six Sigma also gives companies a framework for measuring improvement and helps them focus on what is most important.
What are the four main functions of management?
Management is responsible to plan, organize, direct, and control people and resources. This includes setting goals, developing policies and procedures, and creating procedures.
Management is the ability to direct, coordinate, control, motivate, supervise, train, and evaluate an organization's efforts towards achieving its goals.
The following are the four core functions of management
Planning - Planning refers to deciding what is needed.
Organizing - Organizing involves deciding how things should be done.
Directing - This refers to getting people follow instructions.
Controlling: Controlling refers to making sure that people do what they are supposed to.
Statistics
- As of 2020, personal bankers or tellers make an average of $32,620 per year, according to the BLS. (wgu.edu)
- The profession is expected to grow 7% by 2028, a bit faster than the national average. (wgu.edu)
- 100% of the courses are offered online, and no campus visits are required — a big time-saver for you. (online.uc.edu)
- Our program is 100% engineered for your success. (online.uc.edu)
- The BLS says that financial services jobs like banking are expected to grow 4% by 2030, about as fast as the national average. (wgu.edu)
External Links
How To
How can Lean Manufacturing be done?
Lean Manufacturing processes are used to reduce waste and improve efficiency through structured methods. They were created in Japan by Toyota Motor Corporation during the 1980s. It was designed to produce high-quality products at lower prices while maintaining their quality. Lean manufacturing seeks to eliminate unnecessary steps and activities in the production process. It includes five main elements: pull systems (continuous improvement), continuous improvement (just-in-time), kaizen (5S), and continuous change (continuous changes). It is a system that produces only the product the customer requests without additional work. Continuous improvement is constantly improving upon existing processes. Just-in-time is when components and other materials are delivered at their destination in a timely manner. Kaizen is continuous improvement. This can be achieved by making small, incremental changes every day. Fifth, the 5S stand for sort, set up in order to shine, standardize, maintain, and standardize. These five elements are combined to give you the best possible results.
The Lean Production System
Six key concepts are the basis of lean production:
-
Flow is about moving material and information as near as customers can.
-
Value stream mapping- This allows you to break down each step of a process and create a flowchart detailing the entire process.
-
Five S's: Sort, Shine Standardize, Sustain, Set In Order, Shine and Shine
-
Kanban is a visual system that uses visual cues like stickers, colored tape or stickers to keep track and monitor inventory.
-
Theory of Constraints - Identify bottlenecks in the process, and eliminate them using lean tools such kanban boards.
-
Just-in Time - Send components and material directly to the point-of-use;
-
Continuous improvement - incremental improvements are made to the process, not a complete overhaul.